Catalyst for polymerization of olefins, preparation method thereof and applications
A technology of olefin polymerization and catalyst, which is applied in the field of olefin polymerization, can solve the problems of difficult to obtain synthetic raw materials, complicated synthetic methods, complex structures, etc., and achieve the effect of simple preparation method, high catalytic activity, and cheap and easy-to-obtain raw materials
- Summary
- Abstract
- Description
- Claims
- Application Information
AI Technical Summary
Problems solved by technology
Method used
Image
Examples
preparation example Construction
[0018] The preparation method of the solid catalyst component of the present invention comprises that in the presence of halide, ROH and magnesium powder are contacted and reacted at a molar ratio of 2.0 to 4.0:1, and then TiCl is added 4 Continue to react with tetrahydrofuran to form a titanium-magnesium complex solution. Concentrate the solution, lower the temperature until crystallization occurs, and remove the liquid to obtain a solid catalyst component.
[0019] In the above method, in the titanium-magnesium complex solution obtained after the reaction of ROH and magnesium powder, ethylaluminum chloride can also be added for further reaction, and then the reacted solution is concentrated, cooled to crystallization, and the liquid is removed to obtain a solid catalyst components.
[0020] The reaction temperature of each step of preparing the catalyst is preferably 20-200°C, more preferably 40-100°C.
[0021] During the above catalyst preparation process, the added TiCl ...
example 1
[0033] Preparation of the solid catalyst component described in the present invention.
[0034] A three-necked reaction flask with a mechanical stirring device was filled with N 2 fully permuted, and at N 2 Add 0.5g (20.8mmol) magnesium powder under the airflow, 0.05g of I 2 60ml (89g) of chloroform was added under stirring, and 2.4ml (42.0mmol) of ethanol was added, and the temperature was raised to 61°C for 4 hours of reaction. After cooling down to room temperature, add 1.2ml (10.81mmol) TiCl 4and 12.0ml (148.0mmol) of tetrahydrofuran (THF), heated to 61 ° C for 4 hours to form a Ti-Mg complex solution. The temperature of the solution was lowered to room temperature, concentrated to saturation, cooled to 0°C to -3°C to precipitate crystals, filtered, and the liquid was removed to obtain solid catalyst component A, which contained 2.12% by mass of Ti, 10.90% by mass of Mg, and 17.20% by mass of Cl , OC 2 h 5 26.41 mass%, THF 40.51 mass%, the compositional formula of t...
example 2
[0037] Prepare solid catalyst component by the method for example 1, difference is the ethanol that adds 2.7ml (47.2mmol) in the preparation process, the TiCl of 1.4ml (12.61mmol) 4 , 12.0ml (148.0mmol) of THF, the obtained solid catalyst component B contains Ti 2.31 mass%, Mg 9.60 mass%, Cl 18.03 mass%, OC 2 h 5 27.62 mass%, THF 41.12 mass%, the composition formula of solid catalyst component B is: TiMg 7.16 Cl 8.37 (OC 2 h 5 ) 12.53 (MgCl 2 ) 1.0 11.63(THF)
PUM
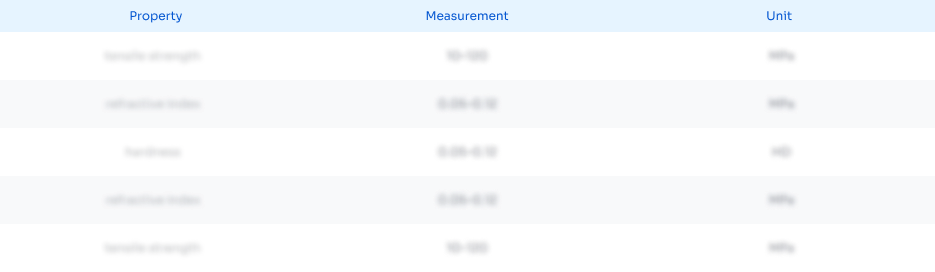
Abstract
Description
Claims
Application Information

- R&D Engineer
- R&D Manager
- IP Professional
- Industry Leading Data Capabilities
- Powerful AI technology
- Patent DNA Extraction
Browse by: Latest US Patents, China's latest patents, Technical Efficacy Thesaurus, Application Domain, Technology Topic, Popular Technical Reports.
© 2024 PatSnap. All rights reserved.Legal|Privacy policy|Modern Slavery Act Transparency Statement|Sitemap|About US| Contact US: help@patsnap.com