Ethylene pyrolysis furnace
A technology of ethylene cracking furnace and radiant furnace tube, which is used in cracking, hydrocarbon cracking to hydrocarbon production, non-catalytic thermal cracking, etc. Covering area, improving radiation heat transfer efficiency, preventing the effect of secondary reaction
- Summary
- Abstract
- Description
- Claims
- Application Information
AI Technical Summary
Problems solved by technology
Method used
Image
Examples
no. 1 Embodiment
[0023] first embodiment :like image 3 As shown, 64 radiation furnace tubes are arranged in each radiation room, and every 16 radiation furnace tubes is a large group, and each radiation room has a total of four groups of such radiation furnace tubes. If there is only one such radiation chamber in the radiation section, the ethylene production capacity of the cracking furnace can reach 60,000-80,000 tons / year; if there are two such radiation chambers in the radiation section, the ethylene production capacity of the cracking furnace can reach 12-160,000 tons / year. Several important dimensions of the cracking furnace are: the distance L between the two radiant furnace tube row planes is 500mm, the distance P between the inlet and outlet pipes is 214mm, the inner diameter of the inlet pipe is 50mm, the inner diameter of the outlet pipe is 61mm, and the length of the radiation chamber is about 15m .
no. 2 Embodiment
[0024] 2nd embodiment :like Figure 4 As shown, 72 radiation furnace tubes are arranged in each radiation room, and each 18 radiation furnace tubes is a large group, and there are four groups of such radiation furnace tubes in each radiation room. If there is only one such radiation chamber in the radiation section, the ethylene production capacity of the cracking furnace can reach 70,000 to 100,000 tons / year; if there are two such radiation chambers in the radiation section, the ethylene production capacity of the cracking furnace can reach 14-200,000 tons / year. Several important dimensions of the pyrolysis furnace are: the spacing L of the tube row is 500mm, the spacing P of the inlet and outlet tubes is 214mm, the inner diameter of the inlet tube is 50mm, the inner diameter of the outlet tube is 61mm, and the length of the radiation chamber is about 17.5m.
no. 3 Embodiment
[0025] 3rd embodiment :like Figure 5 As shown, 80 radiation furnace tubes are arranged in each radiation room, and every 20 radiation furnace tubes is a large group, and there are four groups of such radiation furnace tubes in each radiation room. If there is only one such radiation chamber in the radiation section, the ethylene production capacity of the cracking furnace can reach 90,000 to 110,000 tons / year; if there are two such radiation chambers in the radiation section, the ethylene production capacity of the cracking furnace can reach 180,000 to 220,000 tons / year. Several important dimensions of the pyrolysis furnace are: the spacing L of the tube row is 500mm, the spacing P of the inlet and outlet tubes is 214mm, the inner diameter of the inlet tube is 50mm, the inner diameter of the outlet tube is 61mm, and the length of the radiation chamber is about 19m.
PUM
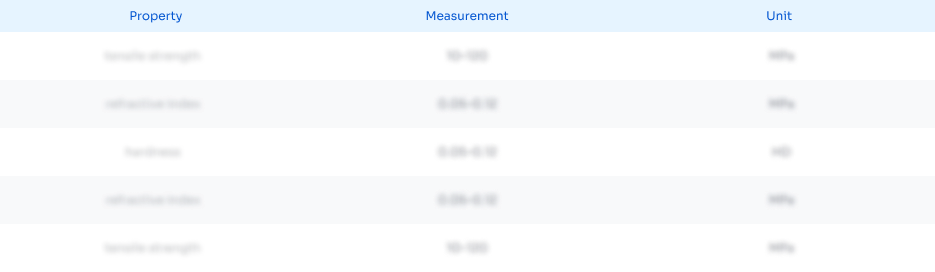
Abstract
Description
Claims
Application Information

- R&D
- Intellectual Property
- Life Sciences
- Materials
- Tech Scout
- Unparalleled Data Quality
- Higher Quality Content
- 60% Fewer Hallucinations
Browse by: Latest US Patents, China's latest patents, Technical Efficacy Thesaurus, Application Domain, Technology Topic, Popular Technical Reports.
© 2025 PatSnap. All rights reserved.Legal|Privacy policy|Modern Slavery Act Transparency Statement|Sitemap|About US| Contact US: help@patsnap.com