Bulk-heating sheet laser pressing method and device
A technology of laser stamping and overall heating, which is applied in laser welding equipment, metal processing equipment, manufacturing tools, etc. It can solve the problems of high equipment investment, complex forming device, and no blank holder, and achieve fast forming speed and high heating temperature. Easy to control, easy to control the effect of heating depth
- Summary
- Abstract
- Description
- Claims
- Application Information
AI Technical Summary
Problems solved by technology
Method used
Image
Examples
Embodiment Construction
[0025] The technical details and implementation of the present invention will be described in detail below in conjunction with the accompanying drawings.
[0026] figure 1 It is a schematic diagram of the forming device of the present invention. First, the surface of the plate 7 is coated with a protective layer 5. The protective layer 5 is made of black paint, graphite or metal coating, with a thickness of 10-100 μm. The function of the protective layer 5 is to generate plasma under laser irradiation and protect the plate from ablation; The protective layer 5 is covered with a constrained layer 4. The constrained layer 4 is made of quartz glass with a thickness of 1-3mm. The constrained layer is almost completely transparent to the laser beam 3, so as to reduce the energy loss of the laser beam 3 and prevent the constrained layer from being burned; Clamp the blank holder 6, the constraining layer 4, the plate 7 coated with the protective layer 5, and the die 8 in the center,...
PUM
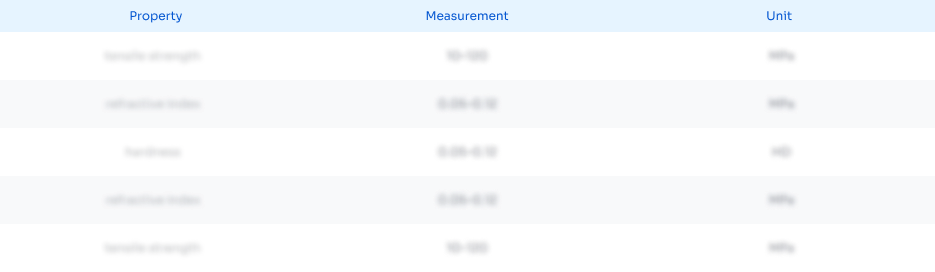
Abstract
Description
Claims
Application Information

- Generate Ideas
- Intellectual Property
- Life Sciences
- Materials
- Tech Scout
- Unparalleled Data Quality
- Higher Quality Content
- 60% Fewer Hallucinations
Browse by: Latest US Patents, China's latest patents, Technical Efficacy Thesaurus, Application Domain, Technology Topic, Popular Technical Reports.
© 2025 PatSnap. All rights reserved.Legal|Privacy policy|Modern Slavery Act Transparency Statement|Sitemap|About US| Contact US: help@patsnap.com