Continuous casting protection slag for high-alumina steel and manufacture method thereof
A technology for continuous casting mold flux and manufacturing method, which is applied to the continuous casting mold flux for high-alumina steel and its manufacturing field, can solve the problems of poor glass, high melting temperature, pollution of the environment, etc., and achieve the effect of good surface quality of the casting billet
- Summary
- Abstract
- Description
- Claims
- Application Information
AI Technical Summary
Problems solved by technology
Method used
Image
Examples
Embodiment 1
[0030] A continuous casting mold flux for high-alumina steel, the percentage ratio of its chemical composition is: CaO+Al 2 o 3 %: 58% and CaO% / Al 2 o 3 %=0.93, SrO: 12%, BaO: 3%, MgO: 1%, flux: Na 2 O: 10%, Li 2 O: 3%, F: 8%, and keep SiO 2 ≤2%. In the ratio of raw materials, it is necessary to make the inevitable impurity SiO 2 The total amount is less than 2%. Reduce SiO in mold flux 2 content, can greatly reduce SiO in slag 2 The activity of the slag is greatly weakened, and the activity of silica is as image 3 shown.
[0031] The method for making the above-mentioned continuous casting mold flux for high aluminum steel comprises the following steps:
[0032] (1) Prepare raw materials according to the following chemical composition percentage ratio: CaO+Al 2 o 3 %: 58% and CaO% / Al 2 o 3 %=0.93, SrO: 12%, BaO: 3%, MgO: 1%, flux ratio: Na 2 O: 10%, Li 2 O: 3%, F: 8%, and keep SiO 2 ≤2%;
[0033] (2) Melting, melting with a water-cooled furnace wall electr...
Embodiment 2
[0039] A continuous casting mold flux for high-alumina steel, the percentage ratio of its chemical composition is: CaO+Al 2 o 3 %: 55% and CaO% / Al 2 o 3 %=0.72, SrO: 10%, BaO: 2%, MgO: 3%, flux: Na 2 O: 14%, Li 2 O: 2%, F: 7%, and keep SiO 2 ≤2%.
[0040] The method for making the above-mentioned continuous casting mold flux for high aluminum steel comprises the following steps:
[0041] (1) Prepare raw materials according to the following chemical composition percentage ratio: CaO+Al 2 o 3 %: 55% and CaO% / Al 2 o 3 %=0.72, SrO: 10%, BaO: 2%, MgO: 3%; flux ratio: Na 2 O: 14%, Li 2 O: 2%, F: 7%, and keep SiO 2 ≤2%;
[0042] (2) Melting, melting with a water-cooled furnace wall electric furnace without lining;
[0043] (3) Water quenching, the slag directly enters the pool and solidifies into a glass body;
[0044] (4) Drying, drying the moisture to prepare for pulverization;
[0045] (5) pulverizing, the powder particle size after pulverizing is that 80% of the u...
Embodiment 3
[0048] as CaO-Al 2 o 3 It is mold flux. In this example, CaO and Al in mold flux 2 o 3 Is the main component, usually (CaO+Al 2 o 3 )% greater than 50%, from the phase diagram when CaO% / Al 2 o 3 When %=0.7~1.3, it is the vitrification formation zone of calcium aluminate, which is the low melting point zone. And when CaO% / Al 2 o 3 % close to 1 is exactly CaO-Al 2 o 3 The eutectic point, where the melting point is the lowest. Therefore, CaO% / Al 2 o 3 %≈1 is ideal, as figure 1 shown. Experimental studies have confirmed that under the same conditions of external components and external flux, when CaO% / Al 2 o 3 The melting temperature of mold flux is the lowest when % is close to 1, such as figure 2 shown. Therefore, in this example, according to CaO% / Al 2 o 3 %≈1 to make mold flux Raw material: CaO+Al 2 o 3 %: 58% and CaO% / Al 2 o 3 %=1, SrO: 5%, BaO: 5%, MgO: 2%, flux: Na 2 O: 12%, Li 2 O: 3%, F: 9%, and keep SiO 2 ≤2%.
[0049] The method for making t...
PUM
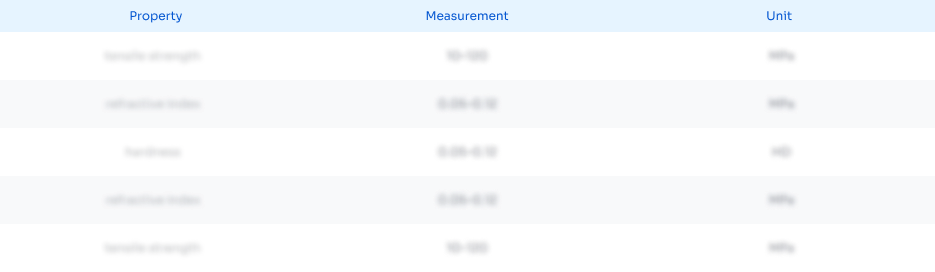
Abstract
Description
Claims
Application Information

- R&D
- Intellectual Property
- Life Sciences
- Materials
- Tech Scout
- Unparalleled Data Quality
- Higher Quality Content
- 60% Fewer Hallucinations
Browse by: Latest US Patents, China's latest patents, Technical Efficacy Thesaurus, Application Domain, Technology Topic, Popular Technical Reports.
© 2025 PatSnap. All rights reserved.Legal|Privacy policy|Modern Slavery Act Transparency Statement|Sitemap|About US| Contact US: help@patsnap.com