Method for preparing microcrystalline foamed glass by titanium-containing blast furnace slag
A technology of microcrystalline foam glass and foam glass, which is applied in the field of comprehensive utilization of metallurgical resources and material preparation. Low utilization rate of titanium blast furnace slag, etc., to achieve low production cost, simple production operation and good product quality
- Summary
- Abstract
- Description
- Claims
- Application Information
AI Technical Summary
Problems solved by technology
Method used
Image
Examples
Embodiment 1
[0022] a, the preparation of glassy raw material: will contain TiO 2 Put the 14% blast furnace slag raw material into an oven at 60°C and dry for 8 hours, grind it finely, pass through a 200-mesh sieve, and then mix the mass ratio of titanium-containing blast furnace slag: micro silica fume: sodium carbonate = 20:80:25 , mixed ingredients; its silicon oxide content is 62.76%, the sodium oxide content is 15.20%, and the calcium oxide content is 6.5%;
[0023] b. Firing in glassy state: put the mixed raw material prepared in step a into a crucible, heat up to 1350°C at a heating rate of 10°C / min and burn for 3 hours, keep it warm for 90min, and quench in water to obtain base glass;
[0024] c, preparation of foam glass raw material: dry and grind calcium carbonate, borax and sodium phosphate respectively to 200 mesh; then dry and grind the glass after water quenching in step b to 180 mesh, Calcium carbonate, borax and sodium phosphate are jointly ground 10min, reach uniform mi...
Embodiment 2
[0029] a, the preparation of glassy raw material: will contain TiO 2 Put 20% blast furnace slag raw material into an oven at 60°C and dry for 8 hours, then grind to 180-200 mesh respectively, and then mix the mass ratio of titanium-containing blast furnace slag:quartzite:sodium carbonate=25:75:25 , mixed ingredients; its silicon oxide content is 61.57%, the sodium oxide content is 15.22%, and the calcium oxide content is 6.92%.
[0030] b. Firing in glassy state: put the mixed raw material prepared in step a into a crucible, heat up to 1350°C at a heating rate of 10°C / min and burn for 3 hours, keep it warm for 90min, and quench in water to obtain base glass;
[0031] c, preparation of foam glass raw material: dry and grind calcium carbonate, borax and sodium phosphate respectively to 200 mesh; then dry and grind the glass after water quenching in step b to 180 mesh, Calcium carbonate, borax and sodium phosphate are grinded together 10min, reach uniform mixing, form foam glas...
Embodiment 3
[0036] a, the preparation of glassy raw material: will contain TiO 2 Put the 26% blast furnace slag raw material in an oven at 60°C for 8 hours, then grind it to 180-200 mesh, and then mix the titanium-containing blast furnace slag:quartz sandstone:sodium carbonate=30:70:25 , mixed ingredients; its silicon oxide content is 59.78%, the sodium oxide content is 15.24%, and the calcium oxide content is 7.55%.
[0037] b. Firing in glassy state: put the mixed raw material prepared in step a into a crucible, heat up to 1350°C at a heating rate of 10°C / min and burn for 3 hours, keep it warm for 90min, and quench in water to obtain base glass;
[0038] c, preparation of foam glass raw material: dry and grind calcium carbonate, borax and sodium phosphate respectively to 200 mesh; then dry and grind the glass after water quenching in step b to 180 mesh, Calcium carbonate, borax and sodium phosphate are grinded together 10min, reach uniform mixing, form foam glass raw material stand-by...
PUM
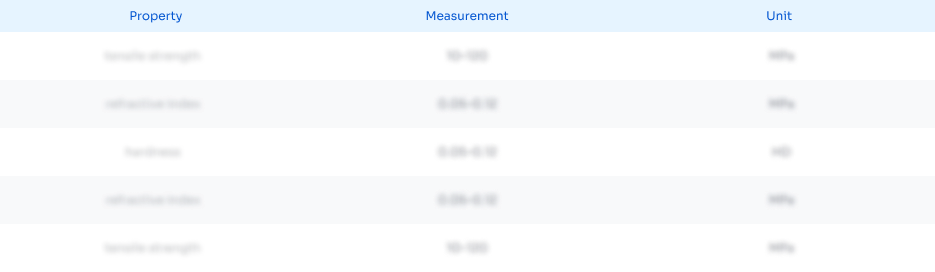
Abstract
Description
Claims
Application Information

- Generate Ideas
- Intellectual Property
- Life Sciences
- Materials
- Tech Scout
- Unparalleled Data Quality
- Higher Quality Content
- 60% Fewer Hallucinations
Browse by: Latest US Patents, China's latest patents, Technical Efficacy Thesaurus, Application Domain, Technology Topic, Popular Technical Reports.
© 2025 PatSnap. All rights reserved.Legal|Privacy policy|Modern Slavery Act Transparency Statement|Sitemap|About US| Contact US: help@patsnap.com