Method for manufacturing front fork of compound material
A production method and bicycle technology, which are applied to bicycle frames, bicycle accessories, steering mechanisms, etc., can solve the problems of increased processing difficulty, high failure rate, and damage to the continuity of composite fibers, so as to simplify the process and solve the problem of qualified rate. , Improve the effect of support strength
- Summary
- Abstract
- Description
- Claims
- Application Information
AI Technical Summary
Problems solved by technology
Method used
Image
Examples
Embodiment Construction
[0022] like figure 2 As shown, the manufacturing method of the composite bicycle front fork of the present invention is mainly that the front fork is formed by changing the traditional three-tube independent winding method of three bobbins into two bobbins.
[0023] As shown in the matching figure, firstly, the composite material is wound into two bobbins respectively, the lower parts of the two bobbins are separated to form two fork tubes 2 of the front fork, and the upper parts of the two bobbins are brought together to form a front fork. Form the standpipe 1 of the front fork, and add a hard metal sheet 4 between the abutment of the two bobbins. Increase the support strength of the standpipe 1; insert a brake hole inner core 5 at the position of the brake hole 3 between the two yarn bobbins, and the brake hole inner core 5 has a brake hole to place the brake; The shape of the front fork is filled with yarn at the joint position; finally, the bobbin is placed in the formin...
PUM
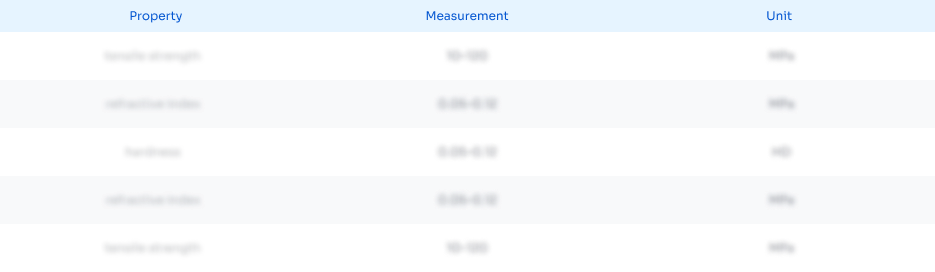
Abstract
Description
Claims
Application Information

- Generate Ideas
- Intellectual Property
- Life Sciences
- Materials
- Tech Scout
- Unparalleled Data Quality
- Higher Quality Content
- 60% Fewer Hallucinations
Browse by: Latest US Patents, China's latest patents, Technical Efficacy Thesaurus, Application Domain, Technology Topic, Popular Technical Reports.
© 2025 PatSnap. All rights reserved.Legal|Privacy policy|Modern Slavery Act Transparency Statement|Sitemap|About US| Contact US: help@patsnap.com