Aluminum alloy car body coloring pervasion weld seam leakage testing technological process
An aluminum alloy car body, coloring penetration technology, applied in the direction of optical testing flaws/defects, detecting the appearance of fluid at leak points, using liquid/vacuum for liquid tightness measurement, etc., can solve problems such as ponding water pollution, Achieve the effects of ensuring surface quality, avoiding rainwater leakage, and facilitating observation
- Summary
- Abstract
- Description
- Claims
- Application Information
AI Technical Summary
Problems solved by technology
Method used
Examples
Embodiment 1
[0013] Eliminate the scale, rust, dust and related factors that affect the flaw detection of the weld to be detected; clean the oily deposits on the weld to be detected with a cleaning agent, and wipe it clean with a clean cloth or cotton gauze; Spray the penetrating agent evenly on the outside to ensure that it is not dry for 10 minutes, and spray it every 2 minutes; observe whether there is leakage on the other side of the weld. If there is leakage, the weld must be repaired to prevent the roof weld The role of rain leakage; after the weld leak test, carry out weld penetration flaw detection, the surface temperature of the detected part should not be higher than 70 ℃, observe whether there are defects in the roof welds, and determine whether the marks are real defects or false defects. Defects are rated against criteria to determine whether to fix them.
Embodiment 2
[0015] Eliminate the scale, rust, dust and related factors that affect the flaw detection of the weld to be detected; clean the oily deposits on the weld to be detected with a cleaning agent, and wipe it clean with a clean cloth or cotton gauze; Spray the penetrant evenly on the outside to ensure that it is not dry for 15 minutes, and spray it every 3 minutes; observe whether there is leakage on the other side of the weld. If there is leakage, the weld must be repaired to prevent the roof weld The role of rain leakage; after the weld leak test, carry out weld penetration flaw detection, the surface temperature of the detected part should not be higher than 70 ℃, observe whether there are defects in the roof welds, and determine whether the marks are real defects or false defects. Defects are rated against criteria to determine whether to fix them.
Embodiment 3
[0017] Eliminate the scale, rust, dust and related factors that affect the flaw detection of the weld to be detected; clean the oily deposits on the weld to be detected with a cleaning agent, and wipe it clean with a clean cloth or cotton gauze; Spray the penetrant evenly on the outside to ensure that it is not dry for 12.5 minutes, and spray it every 2.5 minutes; observe whether there is leakage on the other side of the weld. If there is leakage, the weld must be repaired to prevent the roof The role of weld leakage; after the weld leak test, conduct weld penetration flaw detection, the surface temperature of the detected part should not be higher than 70 ℃, observe whether there are defects in the roof weld, and determine whether the trace is a real defect or a false defect are displayed, and defects are rated against criteria for patching.
PUM
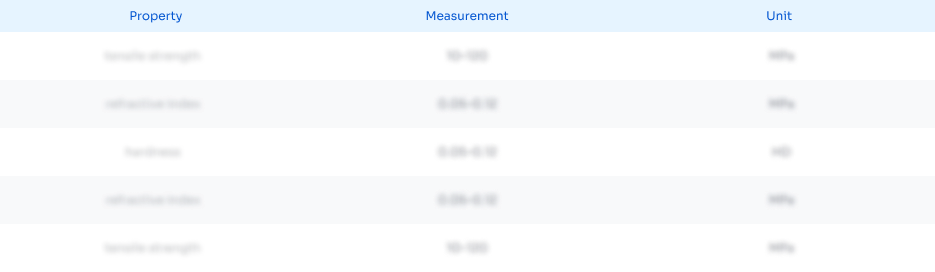
Abstract
Description
Claims
Application Information

- Generate Ideas
- Intellectual Property
- Life Sciences
- Materials
- Tech Scout
- Unparalleled Data Quality
- Higher Quality Content
- 60% Fewer Hallucinations
Browse by: Latest US Patents, China's latest patents, Technical Efficacy Thesaurus, Application Domain, Technology Topic, Popular Technical Reports.
© 2025 PatSnap. All rights reserved.Legal|Privacy policy|Modern Slavery Act Transparency Statement|Sitemap|About US| Contact US: help@patsnap.com