Alloyed aluminum-nickel-chromium-iron composite alloy for final deoxidizing in steel-making
A composite alloy and alloying technology, which is applied in the field of steel alloys and aluminum-nickel-chromium-copper-iron composite alloys, can solve the problems of affecting the refining rate of steel types, affecting the time of steel making, and large fluctuations in yield rate, so as to save time process, increase the steelmaking time, and the effect of low melting point
- Summary
- Abstract
- Description
- Claims
- Application Information
AI Technical Summary
Problems solved by technology
Method used
Examples
Embodiment 1
[0025] In terms of weight percentage, the composition of the aluminum-nickel-chromium-copper-iron composite alloy is as follows: C 0.15; Si 0.8; P 0.023; S0.020; Al 35; Ni 25; Cr20; Cu 15; Fe balance.
[0026] The Al-Ni-Cr-Cu-Fe composite alloy of the present invention is used for the production of 0Cr18Ni9Cu3, and final deoxidation is carried out; the molten steel after the furnace is tapped into the large tank 1 / 5, and all kinds of deoxidizers are added, including the Al-Ni-Cr-Cu of the present invention. Add 1 to 3kg / ton of molten steel to the iron composite alloy, and stop adding when the molten steel is 4 / 5 out of the large tank. The slag should be blocked for tapping. The tapping hole is large, and it must be replaced in time to reduce the flow of steel slag into the molten steel tank. The post-furnace refining lays a good foundation, and the effect is good. The composition and properties of the steel after the furnace are shown in Table 2.
[0027] Table 2
[0028] ...
Embodiment 2
[0030] The difference from Example 1 is that: by weight percentage, the composition of the aluminum-nickel-chromium-copper-iron composite alloy is as follows:
[0031] C 0.24; Si 0.5; P 0.028; S 0.034; Al 10; Ni 20; Cr40; Cu 18; Fe balance.
Embodiment 3
[0033] The difference from Example 1 is that: by weight percentage, the composition of the aluminum-nickel-chromium-copper-iron composite alloy is as follows:
[0034] C 0.3; Si 1.0; P 0.017; S 0.036; Al 12; Ni 20; Cr 30; Cu 28; Fe balance.
PUM
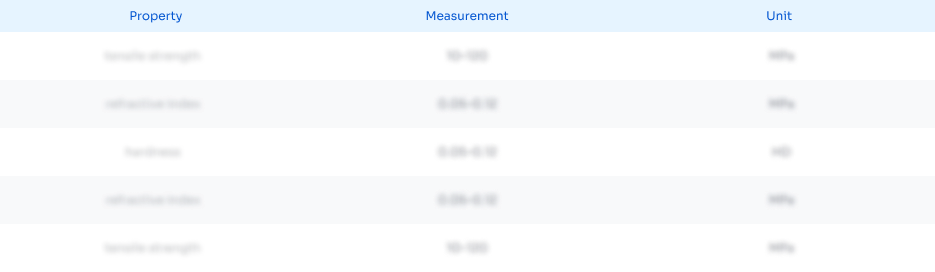
Abstract
Description
Claims
Application Information

- R&D
- Intellectual Property
- Life Sciences
- Materials
- Tech Scout
- Unparalleled Data Quality
- Higher Quality Content
- 60% Fewer Hallucinations
Browse by: Latest US Patents, China's latest patents, Technical Efficacy Thesaurus, Application Domain, Technology Topic, Popular Technical Reports.
© 2025 PatSnap. All rights reserved.Legal|Privacy policy|Modern Slavery Act Transparency Statement|Sitemap|About US| Contact US: help@patsnap.com