Method and grinding machine for profiling a grinding tool
A technology of profile grinding and grinding tools, which is applied to the parts of grinding machine tools, manufacturing tools, grinding/polishing equipment, etc., and can solve the problems of expensive and time-consuming grinding processes
- Summary
- Abstract
- Description
- Claims
- Application Information
AI Technical Summary
Problems solved by technology
Method used
Image
Examples
Embodiment Construction
[0029] exist figure 1 The per se known row-by-row dressing of the grinding tool 1 in the form of a grinding screw can be seen in FIG. In axial section, the grinding screw 1 has a tooth profile 2 which is determined or limited by two tooth flanks 3 and 4 . The first tooth flank 3 and likewise the second tooth flank 4 have a largely rectilinear shape in axial section, but corrections are superimposed on the largely rectilinear course in order to obtain a corresponding coherence in the finished gear wheel. Yoke profile. The two tooth flanks 3 and 4 lie opposite one another as can be seen.
[0030] In order for the tooth profile 2 to have the desired precise shape, a dressing process is necessary, for which a disk-shaped dressing tool 5 is provided. In axial section, the dressing tool 5 has the figure 1 The shape described in , namely a first grinding surface 6 and a second grinding surface 7 , which are used to cooperate with the first tooth flank 3 or the second tooth flank ...
PUM
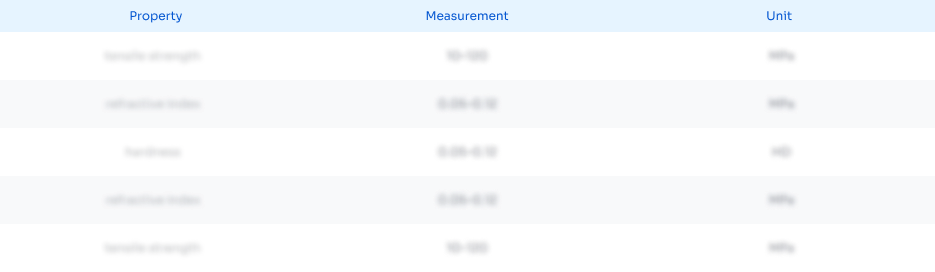
Abstract
Description
Claims
Application Information

- R&D
- Intellectual Property
- Life Sciences
- Materials
- Tech Scout
- Unparalleled Data Quality
- Higher Quality Content
- 60% Fewer Hallucinations
Browse by: Latest US Patents, China's latest patents, Technical Efficacy Thesaurus, Application Domain, Technology Topic, Popular Technical Reports.
© 2025 PatSnap. All rights reserved.Legal|Privacy policy|Modern Slavery Act Transparency Statement|Sitemap|About US| Contact US: help@patsnap.com