Method for producing nano-scale rare earth doping composite oxides sosoloid with low-temperature carbothermic method
A composite oxide, rare earth doping technology, applied in the direction of calcium/strontium/barium oxide/hydroxide, etc., can solve the problems of cumbersome steps, difficult to control particle size, etc., achieve high reactivity, short reaction period, reduce Effects of energy consumption and pollution
- Summary
- Abstract
- Description
- Claims
- Application Information
AI Technical Summary
Problems solved by technology
Method used
Image
Examples
Embodiment 1
[0020] Prepare 0.25M Ca(NO 3 ) 2 , 0.5M Ce(NO 3 ) 3 , 0.625M CaAC 2 Take 15ml of each solution and mix it in a ceramic reactor. Add 15ml of distilled water to further dissolve and mix. Use an electric heating mantle to control the heating temperature to 150℃. The solution changes from sol to gel until self-propagating combustion occurs and releases A large amount of brown gas and fluffy powder are produced. After the gas is dissipated, the powder is collected, that is, the self-combustion precursor powder; weigh an appropriate amount of the precursor powder into a porcelain boat, and calcined in a muffle furnace at 750°C for 2 hours to obtain a calcium oxide-based cerium doped composite Oxide solid solution.
Embodiment 2
[0022] Prepare 0.25M Ca(NO 3 ) 2 , 0.75M La(NO 3 ) 3 , 1.25M CaAC 2 Take 15ml of each solution and mix it in a ceramic reactor. Add 15ml of distilled water to further dissolve and mix. Use an electric heating mantle to control the heating temperature to 140℃. The solution changes from sol to gel until self-propagating combustion occurs and releases A large amount of brown gas produces fluffy powder. After the gas is dissipated, the powder is collected, that is, self-combustion precursor powder; Weigh an appropriate amount of precursor powder into a porcelain boat, calcined in a muffle furnace at 800°C for 1.5 hours to obtain calcium oxide-based lanthanum doping Composite oxide solid solution.
Embodiment 3
[0024] Prepare 0.4M Ca(NO 3 ) 2 , 1.0M Ce(NO 3 ) 3 , 1.0M CaAC 2 Take 15ml of each solution and mix it in a ceramic reactor. Add 15ml of distilled water to further dissolve and mix. Use an electric heating mantle to control the heating temperature to 160℃. The solution changes from sol to gel until self-propagating combustion occurs and releases A large amount of brown gas and fluffy powder are produced. After the gas is dissipated, the powder is collected, that is, self-combustion precursor powder; Weigh an appropriate amount of the precursor powder into a porcelain boat, calcined in a muffle furnace at 900°C for 1 hour to obtain a calcium oxide-based cerium doped composite Oxide solid solution.
PUM
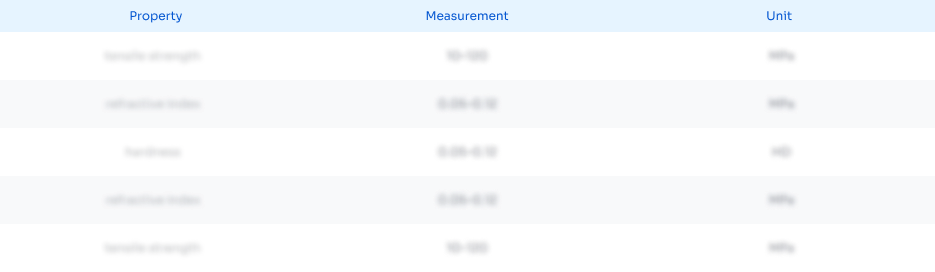
Abstract
Description
Claims
Application Information

- R&D
- Intellectual Property
- Life Sciences
- Materials
- Tech Scout
- Unparalleled Data Quality
- Higher Quality Content
- 60% Fewer Hallucinations
Browse by: Latest US Patents, China's latest patents, Technical Efficacy Thesaurus, Application Domain, Technology Topic, Popular Technical Reports.
© 2025 PatSnap. All rights reserved.Legal|Privacy policy|Modern Slavery Act Transparency Statement|Sitemap|About US| Contact US: help@patsnap.com