Joint structure and boot for joint
A joint structure and joint cover technology, which is applied to elastic couplings, mechanical equipment, couplings, etc., can solve problems such as damage, and achieve the effect of reducing the number of parts and light weight
- Summary
- Abstract
- Description
- Claims
- Application Information
AI Technical Summary
Problems solved by technology
Method used
Image
Examples
Embodiment Construction
[0062] Preferred embodiments of the joint structure and the joint cover according to the present invention will be described in detail below with reference to the accompanying drawings.
[0063] First, the joint structure, which serves as a driving force transmission mechanism for transmitting the driving force from the engine to the tires, will be described below.
[0064] FIG. 1 is a schematic partial perspective view of a joint structure 20 (driving force transmission mechanism) according to an embodiment of the present invention. In FIG. 1, reference numerals 3, 24 denote a cage type constant velocity joint and a spline shaft of a differential gear, respectively. The joint cover 28 is mounted on a part of the outer member 4 of the CV joint 3 and the end of the spline shaft 24 and extends therebetween.
[0065] The cage-type constant velocity joint 3 includes: an outer member 4 having a substantially hemispherical shape with an opening (not shown); and an inner member (not...
PUM
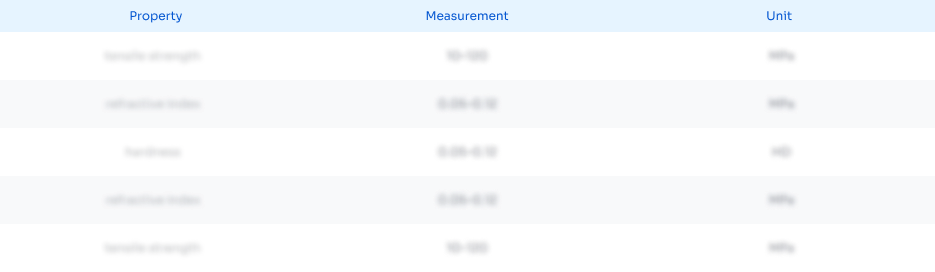
Abstract
Description
Claims
Application Information

- R&D
- Intellectual Property
- Life Sciences
- Materials
- Tech Scout
- Unparalleled Data Quality
- Higher Quality Content
- 60% Fewer Hallucinations
Browse by: Latest US Patents, China's latest patents, Technical Efficacy Thesaurus, Application Domain, Technology Topic, Popular Technical Reports.
© 2025 PatSnap. All rights reserved.Legal|Privacy policy|Modern Slavery Act Transparency Statement|Sitemap|About US| Contact US: help@patsnap.com