Forging bearing straight three-way production method
A manufacturing method and forging technology, which is applied in the field of large-scale straight three-way manufacturing, can solve problems affecting product quality, high material consumption, and great difficulties, and achieve the effects of saving manpower and time, eliminating loose materials, and reducing the processing period
- Summary
- Abstract
- Description
- Claims
- Application Information
AI Technical Summary
Problems solved by technology
Method used
Image
Examples
Embodiment Construction
[0016] The following describes the features of the present invention and other related features in further detail through embodiments in conjunction with the accompanying drawings, so as to facilitate the understanding of those skilled in the industry:
[0017] Such as Figure 1-3 As shown, the numbers 1-5 respectively indicate: blank 1, branch hole 2, interview piece 3, end test piece 4, and main hole 5.
[0018] The method of this embodiment includes the following steps:
[0019] (1) Blank preparation: cut off the head and tail of a qualified steel ingot, and forge it into a forging blank 1 that meets the requirements. Determine the center point of the main punching hole according to the actual shape and size of the required straight tee.
[0020] (2) Forming treatment of straight three-way main holes and supporting holes: forging punching, offset reaming and die positioning are performed at the center point of the main hole punching of the blank 1 Forging and punching are carrie...
PUM
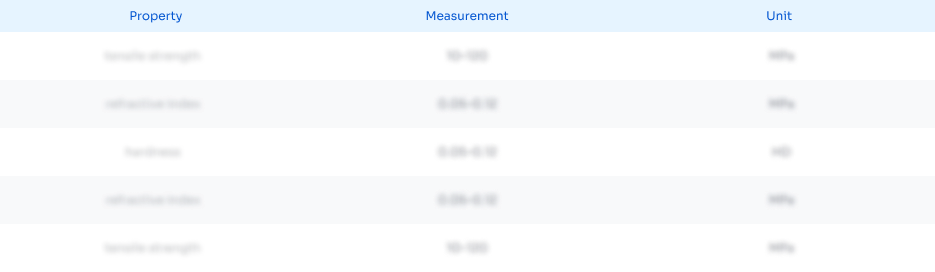
Abstract
Description
Claims
Application Information

- R&D
- Intellectual Property
- Life Sciences
- Materials
- Tech Scout
- Unparalleled Data Quality
- Higher Quality Content
- 60% Fewer Hallucinations
Browse by: Latest US Patents, China's latest patents, Technical Efficacy Thesaurus, Application Domain, Technology Topic, Popular Technical Reports.
© 2025 PatSnap. All rights reserved.Legal|Privacy policy|Modern Slavery Act Transparency Statement|Sitemap|About US| Contact US: help@patsnap.com