Circulating fluid bed boiler furnace possessing heating screen
A circulating fluidized bed and boiler furnace technology, applied in steam boilers, lighting and heating equipment, steam generation, etc., can solve the problems of furnace material concentration, temperature distribution, heat transfer uniformity, and furnace material circulation. Complete combustion and low NOx emissions
- Summary
- Abstract
- Description
- Claims
- Application Information
AI Technical Summary
Problems solved by technology
Method used
Image
Examples
Embodiment 1
[0027] Such as figure 1 and figure 2 As shown, in the furnace of a circulating fluidized bed boiler with a heating screen, three heating screens 3 with the same height as the furnace and equally spaced and parallel to each other are arranged between the furnace air distribution plate 1 and the ceiling 2. The heating screen 3 consists of a membrane wall Composition, the working medium is passed through the membrane wall tube from bottom to top, the upper part of the heating panel 3 is vertical, and the lower part of the membrane wall tube is divided into two parts, which respectively let the tube flow in two directions perpendicular to the surface of the heating panel 3. , forming a "herringbone" space 4 connecting the front and back of the screen. The lower part of the heating screen 3 is laid with a wear-resistant material 6 of the same height as the wear-resistant layer 5 at the lower part of the furnace water wall.
Embodiment 2
[0029] Such as image 3 and Figure 4 As shown, in the furnace of a circulating fluidized bed boiler with a heating screen, a heating screen 3 with the same height as the furnace is arranged between the furnace air distribution plate 1 and the ceiling 2. The heating screen 3 is composed of two membrane walls that are closely attached together. Each membrane wall has only one side facing the combustion space of the furnace; the two membrane walls are fixed with a comb-shaped plate (not shown in the figure) and filled with refractory material 7; the inside of the membrane wall tube is bottom-up There is a working medium, the upper part of the heating screen 3 is vertical, and the lower part keeps two membrane walls close together, divides the width into four equal parts, and alternates the tubes in two directions perpendicular to the surface of the heating screen 3, forming three Connect the "herringbone" space 4 before and after the screen. The wear-resistant material 6 is la...
Embodiment 3
[0031] Such as Figure 5-7 As shown, for a circulating fluidized bed boiler furnace with heating panels, there are three heating panels 3 with the same height as the furnace and the upper part on the same plane between the furnace air distribution plate 1 and the ceiling 2. Each heating panel 3 is composed of two Each membrane wall has only one side facing the furnace combustion space; the two membrane walls are fixed with a comb-shaped plate (not shown in the figure) and filled with refractory material ( Not shown in the figure); there is a working fluid in the membrane wall tube from bottom to top, the upper part of the heating screen 3 is vertical, and the lower part is a square cylindrical space 8 formed by two membrane walls in different directions to allow the tube to surround and synthesize , the cylinder is made of a single-layer membrane wall, and the combustion wind is passed into the column, and the cylinder is provided with an air port (not shown in the figure); th...
PUM
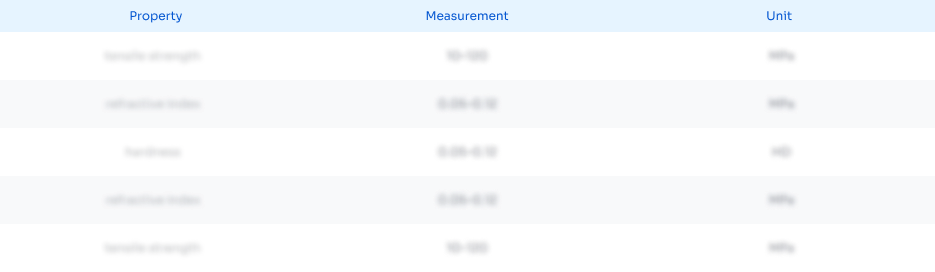
Abstract
Description
Claims
Application Information

- R&D
- Intellectual Property
- Life Sciences
- Materials
- Tech Scout
- Unparalleled Data Quality
- Higher Quality Content
- 60% Fewer Hallucinations
Browse by: Latest US Patents, China's latest patents, Technical Efficacy Thesaurus, Application Domain, Technology Topic, Popular Technical Reports.
© 2025 PatSnap. All rights reserved.Legal|Privacy policy|Modern Slavery Act Transparency Statement|Sitemap|About US| Contact US: help@patsnap.com