Mild technique for separating coal whole components
A full-component, mild technology, applied in the petroleum industry, solid fuel, solid solvent extraction, etc., can solve problems such as unfavorable coal reuse, and achieve the effect of increasing value
- Summary
- Abstract
- Description
- Claims
- Application Information
AI Technical Summary
Problems solved by technology
Method used
Image
Examples
Embodiment 1
[0023] Embodiment 1: In Fig. 1, 1, solid-liquid mixer; 2, extractor; 3, extraction solid-liquid separator; 4, extraction liquid stripper; 5, stripping solid-liquid separator; 6, layering Separator; 7, raffinate coal scrubber; 8, raffinate coal dryer; 9, ultra-pure coal I scrubber; 10, ultra-pure coal I dryer; 11, atmospheric distiller; 12, layered liquid reaction Extractor; 13. Adhesive component dryer; 14. Coarse membrane separator; 15. Fine membrane separator; 16. Atmospheric rectification tower; 17. Vacuum distillation tower; 18. Ultra-pure coal II dryer; 19. Ultrafine mineral dryer; 20. Liquid-liquid mixer.
[0024] For a commercial coal sample with a carbon content of 86.5% (W%, daf), a coal sample of <100 mesh is prepared by crushing, and the whole components are separated according to the following process:
[0025] Put the raw coal into the solid-liquid mixer 1, mix it with the prepared mixed solvent of solvent A and solvent B at a ratio of 100L / kg coal, and then send...
Embodiment 2
[0034] Embodiment 2: To the coal commodity sample that carbon content is 85.0% (W%, daf), make the coal sample of < 120 mesh through pulverization, carry out whole component separation according to the following technological process:
[0035] Put the raw coal into the solid-liquid mixer 1, mix it with the prepared mixed solvent of solvent A and solvent B at a ratio of 50L / kg coal, then send it to the extractor 2, and stir and extract at a pressure of 2atm and a temperature of 20°C for 300min. Then it is sent to solid-liquid separator 3 for solid-liquid separation; the separated solid phase components are sent to washing machine 7 and washed with solvent C at a ratio of 1L / kg solids, and the washed solid phase components are sent to dry In vessel 8, after drying at 0.01 atm and 50°C, the first component, that is, raffinate coal, is separated.
[0036] The liquid-phase extraction liquid of solid-liquid separator 3 is sent into stripper 4, and the solvent C from scrubber 7 is ca...
Embodiment 3
[0044] Embodiment 3: to the coal commodity sample that carbon content is 83.9% (W%, daf), make the coal sample of <300 meshes through pulverization, carry out whole component separation according to the following technological process:
[0045] The raw coal is added to the solid-liquid mixer 1, and the mixed solvent prepared with the raffinate of the atmospheric rectification tower 16 and the recovery solvent A is mixed with the ratio of 150L / kg coal and then sent to the extractor 2. Stir and extract at 100°C for 30 minutes, and then send it to the solid-liquid separator 3 for solid-liquid separation; the separated solid phase components are sent to the scrubber 7 to wash with solvent C at a ratio of 3L / kg solids, and the washed The solid phase components are sent to the drier 8, and after drying at 0.5atm and 120°C, the first component, namely raffinate coal, is separated.
[0046] The liquid-phase extraction liquid of solid-liquid separator 3 is sent into back extractor 4, a...
PUM
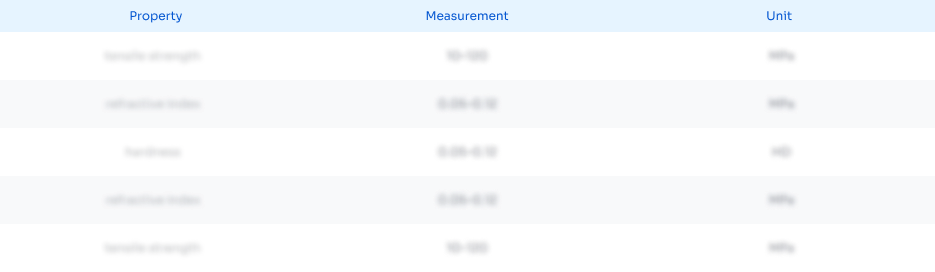
Abstract
Description
Claims
Application Information

- R&D
- Intellectual Property
- Life Sciences
- Materials
- Tech Scout
- Unparalleled Data Quality
- Higher Quality Content
- 60% Fewer Hallucinations
Browse by: Latest US Patents, China's latest patents, Technical Efficacy Thesaurus, Application Domain, Technology Topic, Popular Technical Reports.
© 2025 PatSnap. All rights reserved.Legal|Privacy policy|Modern Slavery Act Transparency Statement|Sitemap|About US| Contact US: help@patsnap.com