Hot-dip galvanizing with electroless ni pre-plating method for controlling thickness of silicon-containing active steel plating
A technology of electroless nickel plating and coating thickness, applied in the field of hot-dip galvanizing of iron and steel parts, can solve the problems of increasing the formation of iron-nickel-zinc ternary zinc slag, the effect of coating growth is not obvious, and reducing the efficiency of nickel use, etc., to achieve the reduction of zinc Effects of loss, bright surface, and reduction of dross generation
- Summary
- Abstract
- Description
- Claims
- Application Information
AI Technical Summary
Problems solved by technology
Method used
Image
Examples
Embodiment 1
[0026] The active steel plate containing silicon 0.04% of chemical composition as following table 1 has carried out the treatment of hot-dip galvanizing after the nickel of pre-electroless plating 4 microns and 3 microns respectively, comprises following process step: (1) carries out chemical process to the surface of silicon-containing steel plate Pre-treatment of nickel plating: Alkaline washing and degreasing of silicon-containing steel sheets in 5% NaCl aqueous solution at a temperature of 60°C; washing with water at a temperature of 50°C; pickling and rust removal in HCl at a temperature of 20°C and a concentration of 15% ;Rinse with clean water at a temperature of 20°C. (2) Electroless nickel plating is carried out on the surface of silicon-containing steel plate, the formula and process adopted are: the nickel salt is NiSO 4 ·6H 2 O, the concentration is 0.1mol / L, and the reducing agent is NaH 2 PO 2 ·H 2 O, the concentration is 0.25mol / L; the complexing agent is C ...
Embodiment 2
[0028] The active steel plate containing silicon 0.09% of chemical composition following table 1 has carried out the treatment of the hot-dip galvanizing after the nickel of pre-electroless plating 4 microns and 3 microns respectively, comprises following process step: (1) carries out chemical coating to the surface of silicon-containing steel plate Pre-treatment of nickel plating: Alkaline washing and degreasing of silicon-containing steel sheets in 5% NaCl aqueous solution at a temperature of 60°C; washing with water at a temperature of 50°C; pickling and rust removal in HCl at a temperature of 25°C and a concentration of 15% ;Rinse with clean water at a temperature of 25°C. (2) Electroless nickel plating is carried out on the surface of silicon-containing steel plate, the formula and process adopted are: the nickel salt is NiSO 4 ·6H 2 O, the concentration is 0.15mol / L, and the reducing agent is NaH 2 PO 2 ·H 2 O, the concentration is 0.3mol / L; the complexing agent is C...
Embodiment 3
[0030] The active steel plate containing silicon 0.18% of chemical composition following table 1 has carried out the treatment of hot-dip galvanizing after the nickel of pre-electroless plating 4 microns and 3 microns respectively, comprises following process step: (1) carries out chemical coating to the surface of silicon-containing steel plate Pre-treatment of nickel plating: Alkaline washing and degreasing of silicon-containing steel sheets in 5% NaCl aqueous solution at a temperature of 70°C; washing with water at a temperature of 50°C; pickling and rust removal in HCl at a temperature of 25°C and a concentration of 15% ;Rinse with clean water at a temperature of 25°C. (2) Electroless nickel plating is carried out on the surface of silicon-containing steel plate, the formula and process adopted are: the nickel salt is NiSO 4 ·6H 2 O, the concentration is 0.2mol / L, and the reducing agent is NaH 2 PO 2 ·H 2 O, the concentration is 0.35mol / L; the complexing agent is C 6 ...
PUM
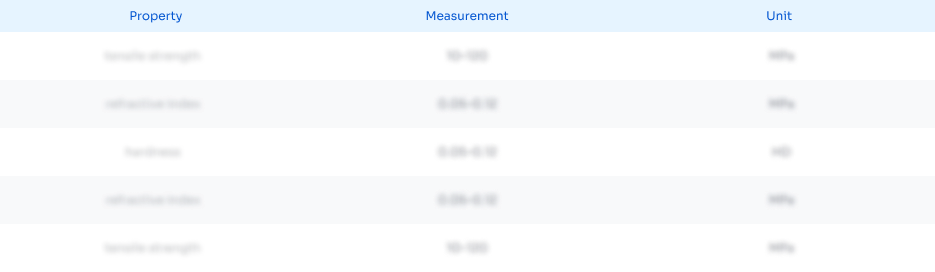
Abstract
Description
Claims
Application Information

- R&D Engineer
- R&D Manager
- IP Professional
- Industry Leading Data Capabilities
- Powerful AI technology
- Patent DNA Extraction
Browse by: Latest US Patents, China's latest patents, Technical Efficacy Thesaurus, Application Domain, Technology Topic, Popular Technical Reports.
© 2024 PatSnap. All rights reserved.Legal|Privacy policy|Modern Slavery Act Transparency Statement|Sitemap|About US| Contact US: help@patsnap.com