Method for preparing inverse suspension polymerization polymethacrylic acid moisture-absorption resin
A technology of polymethacrylic acid, methacrylic acid, applied in the field of hygroscopic materials
- Summary
- Abstract
- Description
- Claims
- Application Information
AI Technical Summary
Problems solved by technology
Method used
Image
Examples
Embodiment 1
[0018] Add 120 g of cyclohexane into the three-necked flask, add 1.3 g of dispersant stearyl phosphoester, and stir at room temperature. 42 grams of methacrylic acid was placed in a beaker, and neutralized with 39.02 grams of 30% sodium hydroxide aqueous solution at -3°C. Dissolve 0.17 g of potassium persulfate and 0.04 g of N,N'-methylenebisacrylamide in 10 g of water; fully dissolve 0.6 g of ethyl hydroxyethyl cellulose in 40 g of water, add initiator and crosslinking agent In the aqueous solution, after mixing evenly, add it into the neutralized methacrylic acid solution to obtain a monomer mixed solution. Raise the temperature of the three-neck flask to 55°C, add the monomer mixture dropwise, finish dropping in 45 minutes, and react at 55°C for 6 hours. After the reaction, cool down to room temperature, filter, wash with methanol, and dry at 110°C to obtain granular polymer Methacrylic hygroscopic resin. The obtained high hygroscopic resin has a moisture absorption rate ...
Embodiment 2
[0020] Add 120 g of cyclohexane into the three-necked flask, add 0.48 g of dispersant stearyl phosphoester, and stir at room temperature. 48 grams of methacrylic acid was placed in a beaker, and neutralized with 48.3 grams of 30% sodium hydroxide aqueous solution at 10°C. Dissolve 0.19 grams of potassium persulfate and 0.04 grams of N, N'-methylenebisacrylamide in 10 grams of water; fully dissolve 1.4 grams of ethyl hydroxyethyl cellulose in 90 grams of water, add initiator and crosslinking agent In the aqueous solution, after mixing evenly, add it into the neutralized methacrylic acid solution to obtain a monomer mixed solution. Raise the temperature of the three-neck flask to 55°C, add the monomer mixture dropwise, and raise the temperature to 65°C after 40 minutes of dripping, and react for 4 hours. After the reaction is completed, lower the temperature to room temperature, filter, wash with methanol, and dry at 100°C to obtain granular Polymethacrylic hygroscopic resin. ...
Embodiment 3
[0022] Add 120 grams of cyclohexane into the three-necked flask, add 2.25 grams of dispersant stearyl phosphoester, and stir at room temperature. 45 grams of methacrylic acid was placed in a beaker, and neutralized with 48.78 grams of 30% sodium hydroxide aqueous solution at -1°C. Dissolve 0.135 grams of potassium persulfate and 0.03 grams of N,N'-methylenebisacrylamide in 10.065 grams of water; fully dissolve 0.9 grams of ethyl hydroxyethyl cellulose in 81 grams of water, add initiator and crosslinking agent In the aqueous solution, after mixing evenly, add it into the neutralized methacrylic acid solution to obtain a monomer mixed solution. Raise the temperature of the three-neck flask to 55°C, add the monomer mixture dropwise, and then raise the temperature to 75°C after 45 minutes, and react for 5 hours. After the reaction, cool down to room temperature, filter, wash with methanol, and dry at 115°C to obtain granular Polymethacrylic hygroscopic resin. The obtained high h...
PUM
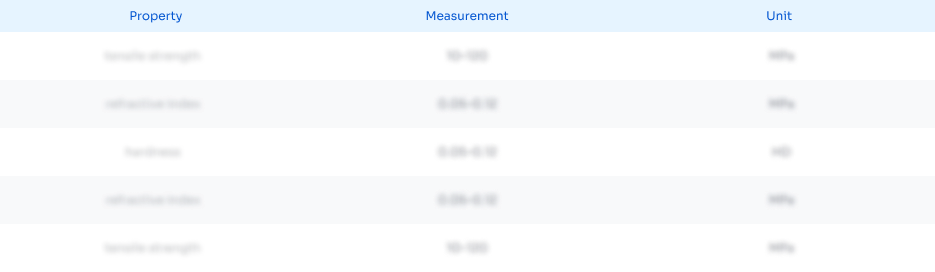
Abstract
Description
Claims
Application Information

- R&D Engineer
- R&D Manager
- IP Professional
- Industry Leading Data Capabilities
- Powerful AI technology
- Patent DNA Extraction
Browse by: Latest US Patents, China's latest patents, Technical Efficacy Thesaurus, Application Domain, Technology Topic, Popular Technical Reports.
© 2024 PatSnap. All rights reserved.Legal|Privacy policy|Modern Slavery Act Transparency Statement|Sitemap|About US| Contact US: help@patsnap.com