Processing method of slot for bolt micro-nick without burr and device thereof
A processing method and burr-free technology, which is applied in the direction of drive devices, metal processing, metal processing equipment, etc., can solve the problems of insufficient precision and burrs at the port, and achieve the effect of high production efficiency, good product quality and easy rotation
- Summary
- Abstract
- Description
- Claims
- Application Information
AI Technical Summary
Problems solved by technology
Method used
Image
Examples
Embodiment 1
[0037] A method for processing screw micro-notches and burr-free slots, comprising the following steps:
[0038] Step 1: Install two milling blades with opposite rotation directions on the periphery of the clamping disc, the first milling blade rotates clockwise (Figure 4-Figure 7), and the second milling blade rotates counterclockwise . The central planes of the two milling blades in the thickness direction are coincident or parallel, and the head of the workpiece can partially intersect with the two milling blades during the rotation of the clamping disk. The center is movable relative to the center of the clamping disc, while the center of the second milling blade is fixed relative to the center of the clamping disc.
[0039] Step 2: The workpiece is clamped on the clamping disc with radially evenly distributed workpiece grooves through the magnetic vibration feeding mechanism, and the head of the workpiece is exposed on the circumference of the clamping disc;
[0040]Ste...
Embodiment 2
[0062] In this embodiment, the first milling blade 13 rotates counterclockwise (Fig. 10-Fig. 13), and the second milling blade 14 rotates clockwise. The first milling insert 13 enters the lower part of the slot where the slot should be milled on the head of the workpiece, and mills an arc-shaped notch at the position where the slot should be milled (Fig. 11, Fig. 14), so that the exit position of the notch is at the workpiece The top of the head does not penetrate another port of the workpiece to be cut, and the first milling blade 13 retreats from the workpiece (Fig. 12) before piercing the other end of the groove to be cut. The other port is unlikely to have glitches. The workpiece continues to rotate with the clamping disc 7. After passing through the second milling blade 14, a slot is milled out. The second milling blade 14 and the first milling blade 13 are on the slot. The milling track intersects on the inner side of the notch (Figure 15), thus forming a micro-notch, a...
PUM
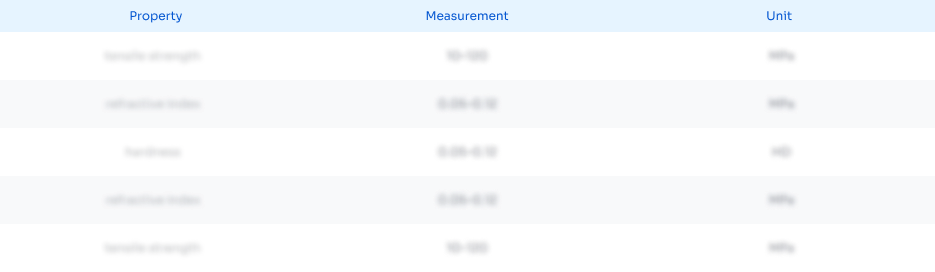
Abstract
Description
Claims
Application Information

- R&D
- Intellectual Property
- Life Sciences
- Materials
- Tech Scout
- Unparalleled Data Quality
- Higher Quality Content
- 60% Fewer Hallucinations
Browse by: Latest US Patents, China's latest patents, Technical Efficacy Thesaurus, Application Domain, Technology Topic, Popular Technical Reports.
© 2025 PatSnap. All rights reserved.Legal|Privacy policy|Modern Slavery Act Transparency Statement|Sitemap|About US| Contact US: help@patsnap.com