Double-frame magnetic suspension control moment gyro
A technology for controlling torque gyroscopes and magnetic levitation, which is applied to the guidance devices of space navigation vehicles, etc., can solve the problems of reducing the service life and reliability of the system by the rotor speed, increasing the weight and volume of the control torque gyroscope, and increasing the power consumption of the system, so as to improve the use of the system. Effects of life and control accuracy, reduction in size and weight, and improved torque resolution
- Summary
- Abstract
- Description
- Claims
- Application Information
AI Technical Summary
Problems solved by technology
Method used
Image
Examples
Embodiment Construction
[0028] As shown in Figure 1, the high-speed motor 4 that the present invention implements needs to be used in pairs and is in the middle part of flywheel rotating shaft 2, and axial hybrid magnetic levitation magnetic bearing 11 needs to be used in pairs and is in the outside of high-speed motor 4, radial hybrid magnetic bearing 5 Need to be used in pairs and located on the upper and lower sides of the high-speed motor 4, the stator part of the high-speed motor 4, the static part of the radial hybrid magnetic bearing 5 and the axial hybrid magnetic levitation magnetic bearing 11 are respectively connected with the upper gyro room 1 and the lower gyro room 12 , the upper gyro room 1 and the lower gyro room 12 are connected with the upper and lower end covers 8 respectively; the rotor part of the high-speed motor 4 and the rotating part of the radial hybrid magnetic bearing 5 are connected with the flywheel shaft 2; the upper end of the radial hybrid magnetic bearing 5 is The rad...
PUM
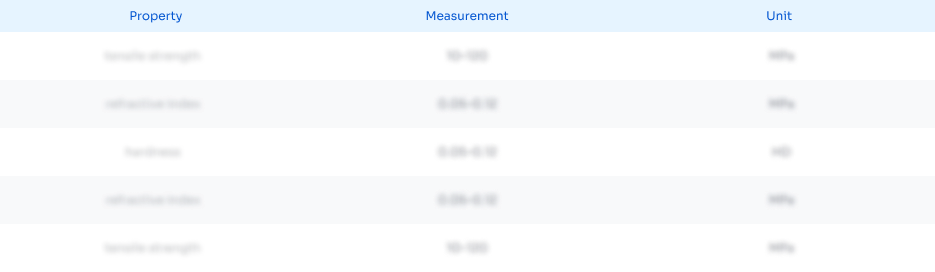
Abstract
Description
Claims
Application Information

- Generate Ideas
- Intellectual Property
- Life Sciences
- Materials
- Tech Scout
- Unparalleled Data Quality
- Higher Quality Content
- 60% Fewer Hallucinations
Browse by: Latest US Patents, China's latest patents, Technical Efficacy Thesaurus, Application Domain, Technology Topic, Popular Technical Reports.
© 2025 PatSnap. All rights reserved.Legal|Privacy policy|Modern Slavery Act Transparency Statement|Sitemap|About US| Contact US: help@patsnap.com