Process for preparing alkylated oil
A technology of alkylate oil and high octane number, which is used in the preparation of alkylate oil, uses ionic liquid as a catalyst to prepare alkylate oil, can solve problems such as low efficiency, and achieve high reaction activity and recycling operation. Simple and energy-saving effect
- Summary
- Abstract
- Description
- Claims
- Application Information
AI Technical Summary
Problems solved by technology
Method used
Image
Examples
Embodiment 1
[0042] The toluenesulfonic acid ionic liquid catalyst of 6.0 grams of pyridine butylsulfonic acid is added in the autoclave with stirring, with N 2 Pressing pressure to 0.5MPa, feed 80g of isobutane and butene-1 mixed raw material, the alkene ratio in the raw material is 6:1. Start stirring, raise the temperature to 70°C within 30min, and use N 2 Ensure the pressure is 1.6MPa, and react for 0.5h. After the reaction, cool down and release the pressure. The reaction solution is poured into a separatory funnel and left to stand for stratification, the lower layer is the catalyst phase, and the upper layer is the alkylated oil phase.
Embodiment 2
[0044] Add 2.0% trifluoromethanesulfonic acid ionic liquid catalyst of 2-butylpyridine propylsulfonate into the autoclave with stirring, and use N 2 Pressing pressure to 0.5MPa, feed 80g of isobutane and butene-1 mixed raw material, the alkene ratio in the raw material is 6:1. Start stirring, raise the temperature to 70°C within 30min, and use N 2 Ensure the pressure is 1.6MPa, and react for 0.5h. After the reaction, cool down and release the pressure. The reaction solution is poured into a separatory funnel and left to stand for stratification, the lower layer is the catalyst phase, and the upper layer is the alkylated oil phase.
Embodiment 3
[0046] The toluenesulfonic acid ionic liquid catalyst of 6.0 grams of 1-butyl imidazole sulfonic acid butyl ester is added in the autoclave with stirring, with N 2 Pressing pressure to 0.5MPa, feed 80g of mixed raw material of isobutane and butene-1, the ratio of alkene in the raw material is 10:1. Start stirring, raise the temperature to 70°C within 30min, and use N 2 Ensure the pressure is 1.6MPa, and react for 0.5h. After the reaction, cool down and release the pressure. The reaction solution is poured into a separatory funnel and left to stand for stratification, the lower layer is the catalyst phase, and the upper layer is the alkylated oil phase.
PUM
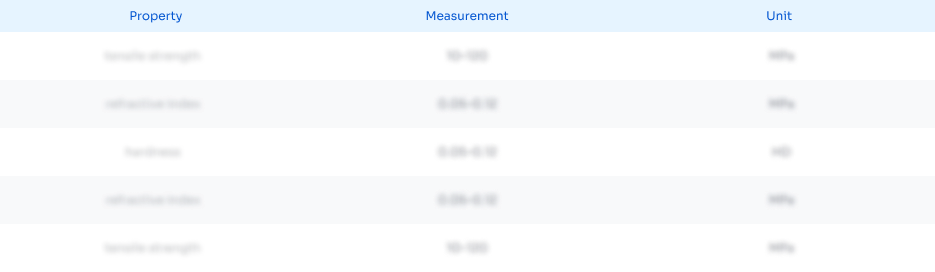
Abstract
Description
Claims
Application Information

- Generate Ideas
- Intellectual Property
- Life Sciences
- Materials
- Tech Scout
- Unparalleled Data Quality
- Higher Quality Content
- 60% Fewer Hallucinations
Browse by: Latest US Patents, China's latest patents, Technical Efficacy Thesaurus, Application Domain, Technology Topic, Popular Technical Reports.
© 2025 PatSnap. All rights reserved.Legal|Privacy policy|Modern Slavery Act Transparency Statement|Sitemap|About US| Contact US: help@patsnap.com