Method of preparing lining for cars
A manufacturing method and bushing technology, applied in metal processing equipment and other directions, can solve the problems of stress concentration and cracks in the flanging process, and achieve the effect of improving the quality rate and service life
- Summary
- Abstract
- Description
- Claims
- Application Information
AI Technical Summary
Problems solved by technology
Method used
Image
Examples
Embodiment Construction
[0019] In order to make the technical means, creative features, goals and effects achieved by the present invention easy to understand, the present invention will be further described below in conjunction with specific embodiments.
[0020] A method for manufacturing a bushing for an automobile, comprising the steps of:
[0021] 1. Blanking: Blanking the steel plate EC with a blanking die and hydraulic equipment to obtain a round material A (see figure 2 );
[0022] 2. Stretching: Stretch the circular material A obtained in step 1 five times with stretching dies and hydraulic equipment with different stretching ratios to obtain a cylindrical part B with a flange (see Figure 7 ), wherein the cylindrical part B' with the flange edge obtained by stretching for the first time (see image 3 ) The stretching ratio is 1:1.3, and the cylindrical part B" with the flange edge obtained by the second stretching (see Figure 4 ) The stretching ratio is 1:1.1, and the cylindrical part ...
PUM
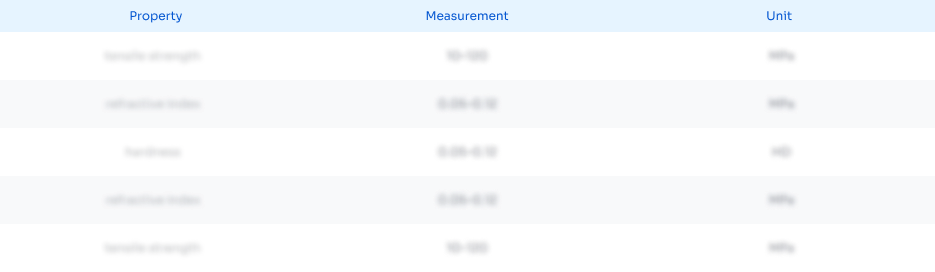
Abstract
Description
Claims
Application Information

- R&D
- Intellectual Property
- Life Sciences
- Materials
- Tech Scout
- Unparalleled Data Quality
- Higher Quality Content
- 60% Fewer Hallucinations
Browse by: Latest US Patents, China's latest patents, Technical Efficacy Thesaurus, Application Domain, Technology Topic, Popular Technical Reports.
© 2025 PatSnap. All rights reserved.Legal|Privacy policy|Modern Slavery Act Transparency Statement|Sitemap|About US| Contact US: help@patsnap.com