Built-in pressure sampling method for differential pressure levelmeter
A differential pressure liquid level gauge, built-in technology, applied in the direction of displaying the liquid level indicator through pressure measurement, can solve problems such as the calibration of the differential pressure liquid level gauge, and achieve the effect of offsetting the liquid level measurement error and saving the liquid storage tank.
- Summary
- Abstract
- Description
- Claims
- Application Information
AI Technical Summary
Problems solved by technology
Method used
Image
Examples
Embodiment 1
[0025] Embodiment 1 is shown in Figure 1: it comprises liquid storage tank 5 (container), differential pressure liquid level gauge 1, positive phase pressure introduction pipe 2, negative phase pressure introduction pipe 3, positive phase pressure introduction pipe 2 and negative phase The pressure introduction pipe 3 is respectively connected to the positive phase end and the negative phase end of the differential pressure liquid level gauge 1 , and the negative phase pressure introduction pipe 3 extends upwards above the highest liquid level in the liquid storage tank 5 . The negative phase pressure guide pipe 3 is pre-filled with the medium to be contained in the liquid storage tank 5, and then the differential pressure liquid level gauge 1 is negatively shifted (zeroed). When it is used to measure a medium with relatively stable physical properties, it is not necessary to inject a solution into the negative phase pressure introduction tube 3 .
Embodiment 2
[0026] Embodiment 2 is shown in Figure 2: it is an improved method of the built-in pressure-taking method of the differential pressure liquid level gauge. The upper end of the phase pressure pipe 3 (higher than the upper limit of the liquid to be measured) has a small hole 6, and a plurality of small holes can be opened. Before the liquid level gauge is used, the medium to be loaded in the future container is pre-injected into the negative phase pressure induction pipe 3, and the liquid level in the negative phase pressure induction pipe 3 rises to the bottom of the small hole 6 (at this time, if the liquid injection continues The level will not rise), and then perform negative shift (zero adjustment) to the differential pressure level gauge 1.
[0027] If it is impossible to judge the liquid injection volume, it is also possible to perform excessive negative migration on the differential pressure liquid level gauge 1 before the liquid injection, that is, the negative migratio...
Embodiment 3
[0032] Embodiment 3 is shown in Figure 3: the differential pressure liquid level gauge 1 is used to measure the interface height between two liquids, and the height of the upper end of the negative phase pressure guiding pipe 3 should be guaranteed to be in the upper liquid (liquid with lower density) . The upper layer liquid in the container can be injected into the negative phase pressure induction pipe 3 in advance, or it can be poured into the negative phase pressure induction pipe 3 by itself after the container is filled with liquid. The liquid level gauge does not need to perform negative migration (zero adjustment), but only needs to calibrate the range (the calculated value can be used for dry calibration when the requirements are not high).
[0033] At this time, Ph=Po+Lρ1+(h-H)ρ1+Hρ2
[0034] ρ1——the density of light liquid in the upper layer ρ2——the density of heavy liquid in the lower layer
[0035] Convert the above formula to get
[0036] Ph-(Po+Lρ1)=hρ1-Hρ1+...
PUM
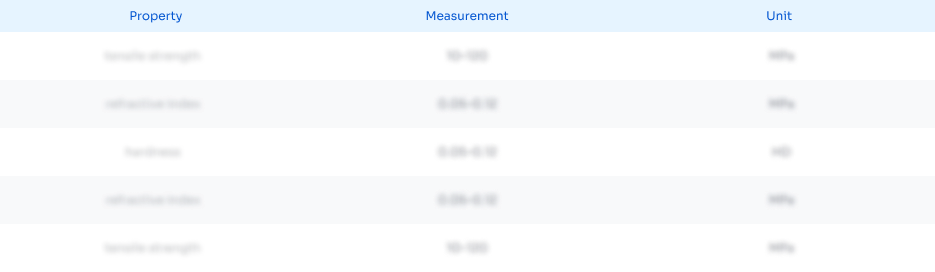
Abstract
Description
Claims
Application Information

- Generate Ideas
- Intellectual Property
- Life Sciences
- Materials
- Tech Scout
- Unparalleled Data Quality
- Higher Quality Content
- 60% Fewer Hallucinations
Browse by: Latest US Patents, China's latest patents, Technical Efficacy Thesaurus, Application Domain, Technology Topic, Popular Technical Reports.
© 2025 PatSnap. All rights reserved.Legal|Privacy policy|Modern Slavery Act Transparency Statement|Sitemap|About US| Contact US: help@patsnap.com