Bulb steel production technology
A technology of production process and production process, applied in the direction of manufacturing tools, metal processing equipment, metal rolling, etc., can solve the problem of bulb flat steel process design, complex parameter calculation, surface scratches and unqualified specifications, and guide device High installation requirements and other issues, to achieve the effect of improving the overall performance of the product, small fluctuations in the size of the arc, and uniform force
- Summary
- Abstract
- Description
- Claims
- Application Information
AI Technical Summary
Problems solved by technology
Method used
Image
Examples
Embodiment Construction
[0017] The present invention is characterized by adopting symmetrical rolling and straightening followed by splitting process, and its production process is: steel billet → heating → symmetrical rolling → straightening → splitting, each pass of the rolling mill consists of two symmetrical and equal Spherical flat steel pass configuration.
[0018] The technical characteristics of the present invention are:
[0019] 1) The number of rolling passes is 9 to 13;
[0020] 2) Pass design:
[0021] a) Roll pass adopts symmetrical design;
[0022] b) The finished hole and the re-front hole of the finished product adopt the ball head opening pass type, and the ball head side of the finished product front hole is open. Defects, ultimately ensuring the precise molding of the ball head and the outer surface of the ball head;
[0023] c) As shown in the figure, the inclination of the web 1 of the finished hole, the finished front hole, and the finished front hole of the roll is 4% to 7...
PUM
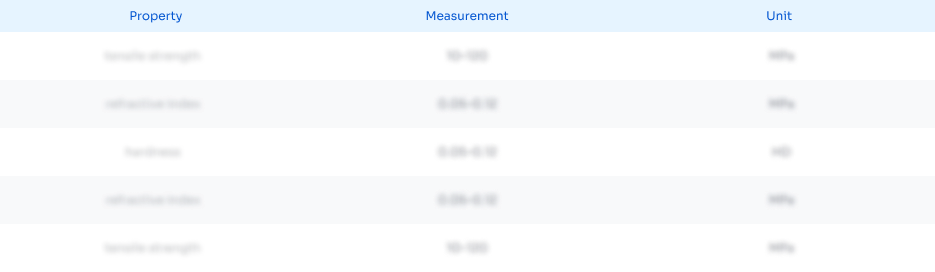
Abstract
Description
Claims
Application Information

- Generate Ideas
- Intellectual Property
- Life Sciences
- Materials
- Tech Scout
- Unparalleled Data Quality
- Higher Quality Content
- 60% Fewer Hallucinations
Browse by: Latest US Patents, China's latest patents, Technical Efficacy Thesaurus, Application Domain, Technology Topic, Popular Technical Reports.
© 2025 PatSnap. All rights reserved.Legal|Privacy policy|Modern Slavery Act Transparency Statement|Sitemap|About US| Contact US: help@patsnap.com