Micro-crystallizing glass-ceramic composite board and producing method thereof
A technology of glass-ceramic and production method, which is applied in the field of building materials, can solve the problems of barium carbonate poisonous, rising cost of glass raw materials, etc., and achieve the effect of reducing the cost of raw materials
- Summary
- Abstract
- Description
- Claims
- Application Information
AI Technical Summary
Problems solved by technology
Method used
Examples
Embodiment 1
[0022] According to the composition 1 in Table 1, a homogeneous batch is prepared and melted into a homogeneous glass melt at a temperature of 1350-1580°C. The glass melt is poured into water, quenched into slag, and the slag particles with a particle size of 0.5-6.5 mm are coarsely sieved for use. Put the glass slag particles obtained by the above method on the ceramic tiles that have been fired at high temperature, apply fixative liquid to fix them, and then send them to the roller kiln to raise the temperature at a rate of no more than 900°C / hour. After 900°C, the slag particles It starts to melt and merge with each other, and the surface of the slag piled up obviously sinks, that is, it obviously starts to sinter, and it is raised to 1200°C for a period of time to keep it for a period of time to fully sinter, and then the temperature is lowered and annealed to cool, and the milky glass-ceramic composite plate is obtained. .
Embodiment 2
[0024] Example 2 is carried out according to the steps of Example 1, but the composition of the glass must be changed from composition 1 in Table 1 to composition 2, and 1% NiO needs to be added in addition, so that brown glass-ceramics with an appearance similar to natural stone can be obtained - Ceramic composite panels.
Embodiment 3
[0026] Embodiment 3 is carried out according to the various steps of embodiment 1, but the composition of the glass must be changed from composition 1 in the above table 1 to composition 3, and additionally 0.5% Co 2 o 3 , can produce a blue glass-ceramic-ceramic composite plate with an appearance similar to natural stone.
PUM
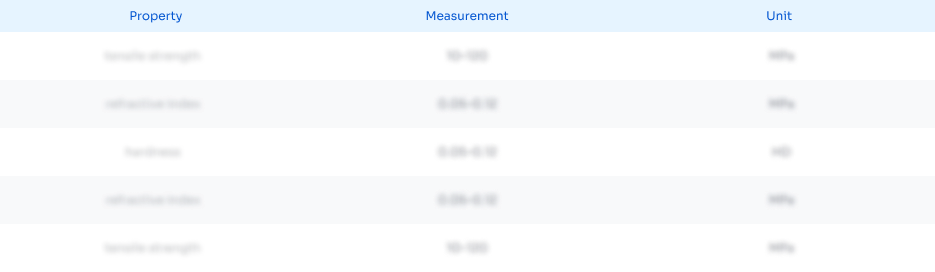
Abstract
Description
Claims
Application Information

- R&D Engineer
- R&D Manager
- IP Professional
- Industry Leading Data Capabilities
- Powerful AI technology
- Patent DNA Extraction
Browse by: Latest US Patents, China's latest patents, Technical Efficacy Thesaurus, Application Domain, Technology Topic, Popular Technical Reports.
© 2024 PatSnap. All rights reserved.Legal|Privacy policy|Modern Slavery Act Transparency Statement|Sitemap|About US| Contact US: help@patsnap.com