Acrylic shrinkable fiber
A shrinkage, acrylic technology, applied in the field of fleece fabric products, can solve the problems of not being able to obtain fleece fabric products with excellent appearance, difficulty in shrinking function, and failing to take into account the dyeing shrinkage function.
- Summary
- Abstract
- Description
- Claims
- Application Information
AI Technical Summary
Problems solved by technology
Method used
Examples
manufacture example 1
[0053] Put 2920g of dimethylformamide (DMF) produced by Nissan Chemical Co., Ltd., 800g of acrylonitrile (AN) produced by Asahi Kasei Co., Ltd., and 120g of methyl acrylate (MA) produced by Toagosei Co., Ltd. into a pressure-resistant polymerization reactor with a capacity of 5L 160 g of a 50% aqueous solution of sodium 2-acrylamide-2-methylpropanesulfonate (SAM) produced by Toagosei Co., Ltd. was replaced with nitrogen. The temperature in the polymerizer was adjusted to 55° C., 5 g of 2,2-azobis(2,4-dimethylvaleronitrile) (AIVN) was charged as an initiator, and polymerization was started. Add 10g AIVN in the middle, polymerize for 2 hours, then be warming up to 70 ℃, polymerize for 10 hours, obtain the 25% solution (DMF / water mixed solvent) of copolymer (AN / MA / SAM=80 / 12 / 8 (weight ratio)) ).
[0054] Take the above solution with a copolymer concentration of 25% as the spinning stock solution, pass the spinning stock solution through a 0.08mmΦ, 2000-hole spinneret, and spray i...
manufacture example 2~10
[0056] Acrylic shrinkable fibers having a fineness shown in Table 1 were produced in the same manner as in Production Example 1 except that the composition of the copolymer was changed to the ratio shown in Table 1 (Production Examples 2 to 9). In addition, except that the composition of the copolymer is the ratio shown in Table 1, polymerization is carried out in the same polymerization method as in Production Example 1, and the same method as in Production Example 1 is carried out except passing through a spinneret with 0.12mmΦ and 800 holes. Spinning was carried out by the same method as in Production Example 1, and the acrylic shrinkable fiber of Production Example 10 was produced in the same manner as Production Example 1.
[0057] [Table 1]
[0058]
Embodiment 1~11 and comparative example 1~4
[0060] Acetic acid and sodium acetate were added to 200cc of 2.5% omf malachite green dyeing bath to make the concentrations 0.05g / L and 0.02g / L, and the pH was adjusted to 3-4. 1 g of the arbitrary shrinkable fibers obtained in Production Examples 1 to 10 were dyed for 60 minutes using the dye bath under the conditions described in Table 2, respectively. Table 2 shows the workability at this time, the relative saturation value, and the measurement results of the shrinkage rate at 130° C. dry heat treatment for 5 minutes after dyeing.
[0061] [Table 2]
[0062] Example
serial number
in use
fiber
Dyeing temperature (℃)
relative saturation value
Residue after dyeing
Shrinkage(%)
Example 1
Manufacturing example 1
○
60
0.4
24
Example 2
Manufacturing example 1
○
70
0.8
21
Example 3
Manufacturing example 3
○
...
PUM
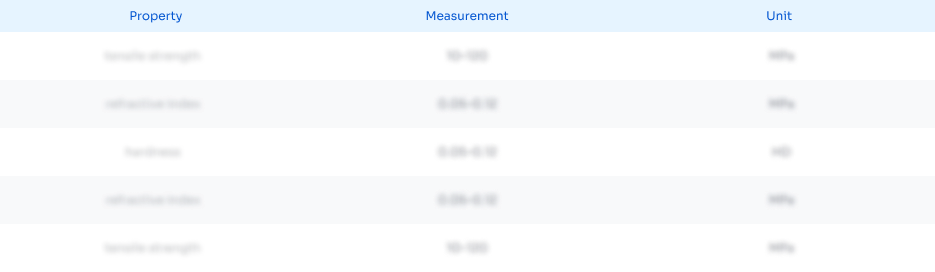
Abstract
Description
Claims
Application Information

- Generate Ideas
- Intellectual Property
- Life Sciences
- Materials
- Tech Scout
- Unparalleled Data Quality
- Higher Quality Content
- 60% Fewer Hallucinations
Browse by: Latest US Patents, China's latest patents, Technical Efficacy Thesaurus, Application Domain, Technology Topic, Popular Technical Reports.
© 2025 PatSnap. All rights reserved.Legal|Privacy policy|Modern Slavery Act Transparency Statement|Sitemap|About US| Contact US: help@patsnap.com