Method for preparing polyether for polycarboxylic acid series concrete additive
A technology for concrete admixtures and polycarboxylates, which is applied in the field of preparation of polyethers for polycarboxylate concrete admixtures, and can solve the problem of increasing the synthesis process route of polycarboxylate concrete admixtures, reducing the quality of raw materials, and polyether molecules. Short chain and other problems, to achieve the effect of superior product quality, improved quality, and narrow molecular weight distribution
- Summary
- Abstract
- Description
- Claims
- Application Information
AI Technical Summary
Problems solved by technology
Method used
Image
Examples
Embodiment 1
[0039] Replace the whole set of equipment with nitrogen (N2), add 3193.30kg hydroxyethyl acrylate, 18.83kgNaOH and 31.93kg1, 4-naphthoquinone to the loop reactor pre-reactor (R-2202), vacuumize (-750mmHg) and heat up to 100 Dehydrate at ℃ for 50 minutes, fill the pre-reactor with N2 to make the pressure of the pre-reactor reach 0.3Mpa, start the small circulation pump (P-2214), and press in 20.71kg of ethylene oxide at the same time to start the reaction for 2 hours; then turn on the large circulation pump (P-2204), press Add ethylene oxide into the reactor at a rate of 3762.70kg / h, polymerize at 160°C and a pressure of 0.3Mpa, maintain the feeding and reaction for 5h, stop adding ethylene oxide, and continue to circulate and mature for 5min; When the pressure no longer decreases, the reaction is over, and the vacuum is turned on to remove free ethylene oxide in the reactor and passed into the polyether tail gas treatment tower for water washing treatment, and the tail gas is d...
Embodiment 2
[0041] Replace the whole set of equipment with nitrogen (N2), add 2863.08kg hydroxyethyl methacrylate, 14.37kgNaOH and 13.32kg1, 4-benzoquinone to the loop reactor pre-reactor (R-2202), vacuumize (-750mmHg) to raise the temperature Dehydrate at 100°C for 50 minutes, fill the pre-reactor with N2 to make the pressure of the pre-reactor reach 0.3Mpa, start the small circulation pump (P-2214), and press 15.81kg of ethylene oxide at the same time to start the reaction for 2 hours; then turn on the large circulation pump (P-2204) , add ethylene oxide to the reactor at a rate of 3190.52kg / h, polymerize at 160°C and a pressure of 0.3Mpa, keep feeding and reacting for 6 hours, stop adding ethylene oxide, and continue to circulate for 7 minutes; when the reaction When the pressure in the reactor no longer decreases, the reaction is over, and the vacuum is turned on to remove the free ethylene oxide in the reactor and passed into the polyether tail gas treatment tower for water washing tr...
Embodiment 3
[0043] Replace the whole set of equipment with nitrogen (N2), add 1431.54kg hydroxypropyl acrylate, 10.29kgNaOH and 3.58kg1, 4-benzoquinone to the loop reactor pre-reactor (R-2202), vacuumize (-750mmHg) and raise the temperature to 100 Dehydrate at ℃ for 50 minutes, fill the pre-reactor with N2 to make the pressure of the pre-reactor reach 0.3Mpa, start the small circulation pump (P-2214), and press in 11.32kg of ethylene oxide at the same time to start the reaction for 2 hours; then turn on the large circulation pump (P-2204), press Add oxyalkylene into the reactor at a rate of 2938.30kg / h, polymerize at 160°C and a pressure of 0.3Mpa, maintain the feeding and reaction for 7h, stop adding ethylene oxide, and continue to circulate and mature for 8min; When it decreases again, the reaction ends, and the vacuum is opened to remove free ethylene oxide in the reactor and passed into the polyether tail gas treatment tower for water washing treatment, and the tail gas is discharged i...
PUM
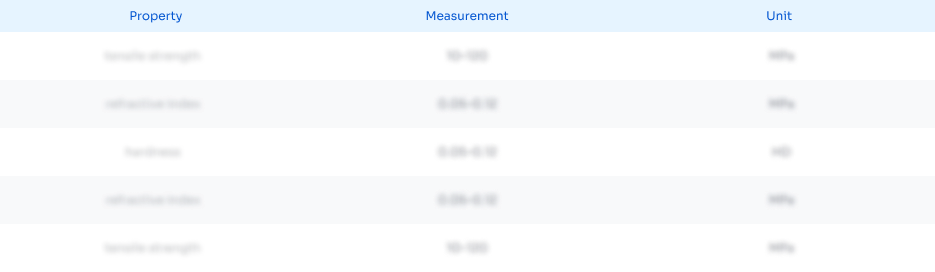
Abstract
Description
Claims
Application Information

- R&D
- Intellectual Property
- Life Sciences
- Materials
- Tech Scout
- Unparalleled Data Quality
- Higher Quality Content
- 60% Fewer Hallucinations
Browse by: Latest US Patents, China's latest patents, Technical Efficacy Thesaurus, Application Domain, Technology Topic, Popular Technical Reports.
© 2025 PatSnap. All rights reserved.Legal|Privacy policy|Modern Slavery Act Transparency Statement|Sitemap|About US| Contact US: help@patsnap.com