Oxidation method and equipment for spent caustic in petrochemistry equipment
A petrochemical and waste lye technology, applied in chemical instruments and methods, oxidation treatment of sludge, oxidized water/sewage treatment, etc., can solve problems such as leakage of hot waste lye, and reduce investment costs, investment costs and equipment The effect of minimizing operational hazards
- Summary
- Abstract
- Description
- Claims
- Application Information
AI Technical Summary
Problems solved by technology
Method used
Image
Examples
Embodiment Construction
[0020] The flow chart of Fig. 1 shows a device for wet oxidation of spent lye in a petrochemical plant according to the prior art. The waste lye (1) is transferred by a high-pressure pump (2). Then, by introducing air or oxygen (3), a liquid-gas mixture (4) composed of waste lye and oxygen-containing gas is generated. It is preheated by the input / output heat exchanger (5) and introduced into the reactor (6) for oxidation. In order to increase the reactor temperature additionally, hot steam can be introduced into the reactor (7). After a residence time dependent on temperature and pressure, the liquid-gas mixture (8) consisting of oxidized alkali and waste gas is led out of the reactor, pre-cooled through the input / output heat exchanger (5), and is cooled The liquid (10) is finally cooled in the second heat exchanger (9). The waste gas (12) is separated from the oxidized lye (13) in the separator (11).
[0021] The flowchart of Figure 2 shows an embodiment of the present invention....
PUM
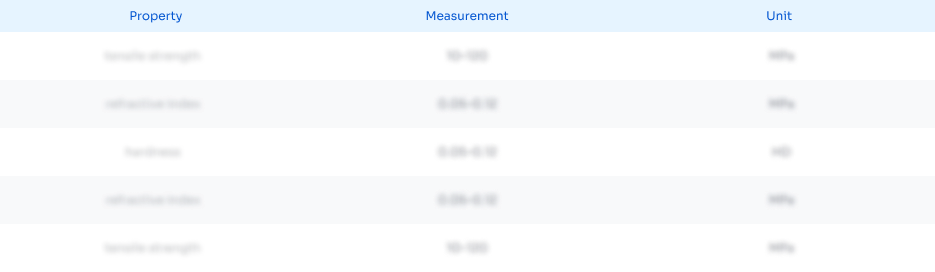
Abstract
Description
Claims
Application Information

- R&D Engineer
- R&D Manager
- IP Professional
- Industry Leading Data Capabilities
- Powerful AI technology
- Patent DNA Extraction
Browse by: Latest US Patents, China's latest patents, Technical Efficacy Thesaurus, Application Domain, Technology Topic, Popular Technical Reports.
© 2024 PatSnap. All rights reserved.Legal|Privacy policy|Modern Slavery Act Transparency Statement|Sitemap|About US| Contact US: help@patsnap.com