Resin mixture and glass reinforced plastic section bar prepared thereby
A technology for glass fiber reinforced plastic profiles and mixed materials, applied in the field of glass fiber reinforced plastic profiles, can solve the problems that the paint texture is not uniform and wear-resistant, can only be painted or sprayed, and the color of the profiles is monotonous. The effect of the market effect
- Summary
- Abstract
- Description
- Claims
- Application Information
AI Technical Summary
Problems solved by technology
Method used
Examples
Embodiment 1
[0010] 10 parts by weight of unsaturated polyester resin HS106 and 0.4 parts by weight of low shrinkage agent polyvinyl acetate resin SW7415, 2 parts by weight of filler calcium carbonate, 0.05 parts by weight of low-temperature curing agent dibenzoyl peroxide, 0.05 parts by weight Mix parts by weight of high-temperature curing agent tert-butyl peroxybenzoic acid resin butyl ester, 0.05 parts by weight of release agent MR-2811, and 0.02 parts by weight of pigment powder, and then add an appropriate amount of coupling agent and ultraviolet absorber to prepare Resin compound.
[0011] Fiberglass yarn, fiberglass cloth, and fiberglass mat are then dipped into the resin mix. This process already has production line equipment, mainly including glass fiber display racks, reinforcement material drying boxes, dipping tanks, mold tables, racks, tractors, cutting saws, and profile turning tables. Now the production line has reached program control, automatic cutting, automatic flipping...
Embodiment 2
[0014] 10 parts by weight of unsaturated polyester resin HS106 and 1 part by weight of low-shrinkage agent polyvinyl acetate resin PV161, 8 parts by weight of filler calcium carbonate, low-temperature curing agent dibenzoyl peroxide of 0.1 parts by weight, 0.1 parts by weight Mix parts by weight of high-temperature curing agent tert-butyl peroxybenzoate, 0.1 parts by weight of release agent MR-2811, and 0.2 parts by weight of pigment powder, and then add an appropriate amount of coupling agent and ultraviolet absorber to prepare Resin compound. Fiberglass yarn, fiberglass cloth, and fiberglass mat are then dipped into the resin mix. Then it is molded under the conditions of 80°C for the first stage, 130°C for the second stage, and 128°C for the third stage. After traction, pultrusion, and finally automatic cutting to obtain the product, the traction speed is 320mm / min.
Embodiment 3
[0016] 10 parts by weight of unsaturated polyester resin HS106 and 2 parts by weight of low shrinkage agent polyvinyl acetate resin SW7415, 10 parts by weight of filler aluminum hydroxide, 0.2 parts by weight of low-temperature curing agent dibenzoyl peroxide, 0.2 parts by weight of high-temperature curing agent tert-butyl peroxybenzoate, 0.2 parts by weight of release agent MR-2811, and 0.4 parts by weight of pigment are mixed, and then an appropriate amount of coupling agent and ultraviolet absorber are added to make a resin Mixture. Fiberglass yarn, fiberglass cloth, and fiberglass mat are then dipped into the resin mix. Then it is molded under the conditions of 80°C for the first stage, 130°C for the second stage, and 128°C for the third stage. After traction, pultrusion, and finally automatic cutting to obtain the product, the traction speed is 320mm / min.
PUM
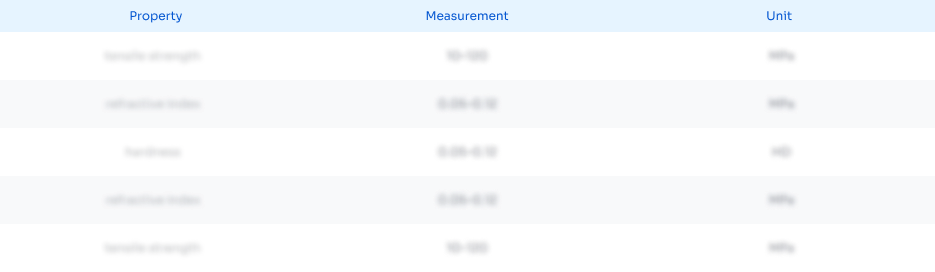
Abstract
Description
Claims
Application Information

- Generate Ideas
- Intellectual Property
- Life Sciences
- Materials
- Tech Scout
- Unparalleled Data Quality
- Higher Quality Content
- 60% Fewer Hallucinations
Browse by: Latest US Patents, China's latest patents, Technical Efficacy Thesaurus, Application Domain, Technology Topic, Popular Technical Reports.
© 2025 PatSnap. All rights reserved.Legal|Privacy policy|Modern Slavery Act Transparency Statement|Sitemap|About US| Contact US: help@patsnap.com