Foamed sheet for reflectors, reflectors, and process for production of the sheet
A foamed sheet, a manufacturing method technology, applied in chemical instruments and methods, diffusing elements, instruments, etc., can solve the problems of poor thermoformability, wrinkles, and reflective plates entering cracks, etc., to achieve the effect of improving light reflection performance
- Summary
- Abstract
- Description
- Claims
- Application Information
AI Technical Summary
Problems solved by technology
Method used
Image
Examples
Embodiment 1~7、 comparative example 1~3
[0100] A tandem type extruder with a diameter of 90mm is prepared by connecting a second-stage single-screw extruder (diameter: 115mm) to the front end of the first-stage single-screw extruder (diameter: 90mm) Single-screw extruder, the former extruder is used as the first extruder, and the latter extruder is used as the second extruder. On the other hand, a confluence die head and the confluence die head connected The co-extrusion die head composed of a ring die head is prepared by connecting the first-stage extruder and the second extruder of the first extruder to the confluence die head of the co-extrusion die head Manufacturing device.
[0101] Next, in the first-stage extruder of the first extruder, a predetermined amount of polypropylene resin (trade name "PF814" manufactured by Sangoroma Company) as shown in Table 1 was sequentially supplied with refractive index : 1.5). A masterbatch containing rutile titanium dioxide (masterbatch) (manufactured by Dainichi Seiki Co., Ltd....
Embodiment 8、9
[0110] The manufacturing apparatus used in Example 1 was prepared. Next, in the first-stage extruder of the first extruder, polypropylene resin (trade name "PF814" manufactured by Sangoroma Co., Ltd.) was sequentially supplied in accordance with the prescribed amount shown in Table 1. : 1.5). A masterbatch containing rutile-type titanium dioxide in a polypropylene resin (trade name "PL500A" manufactured by Sanya Roman Co., Ltd., refractive index: 1.5) (trade name manufactured by Toyo Ink Manufacturing Co., Ltd.) "PPM 1KB 622WHT FD", titanium dioxide (refractive index: 2.76): 70% by weight, polypropylene resin: 30% by weight), and a masterbatch containing a mixture of sodium bicarbonate and citric acid in the resin (Colleriant ( Clarion Corporation’s product name "Hydroxylu (Hydrosol) HK-70", a mixture of sodium bicarbonate and citric acid 70% by weight), melted and kneaded at 200°C to form a foamable polypropylene resin combination Things. In addition, the blending ratios of the p...
Embodiment 10、11
[0118] Prepare the tandem extruder used in Example 1 and a single-screw extruder with a diameter of 90 mm for the second machine. The former extruder is used as the first extruder and the latter extruder is used as the second extruder. The extruder and the third extruder, on the other hand, prepare a co-extrusion die consisting of a confluence die and an annular die connected to the confluence die, and prepare the first stage of the first extruder A manufacturing device formed by connecting an extruder, a second extruder, and a third extruder to the confluence die of the co-extrusion die.
[0119] Next, in the first-stage extruder of the first extruder, polypropylene resin (trade name "PF814" manufactured by Sangoroma Co., Ltd.) was sequentially supplied in accordance with the prescribed amount shown in Table 1. : 1.5). A masterbatch containing rutile titanium dioxide (trade name "SSC-04B384" manufactured by Dainichi Seika Co., Ltd.) in a polypropylene resin (trade name "PL500A" m...
PUM
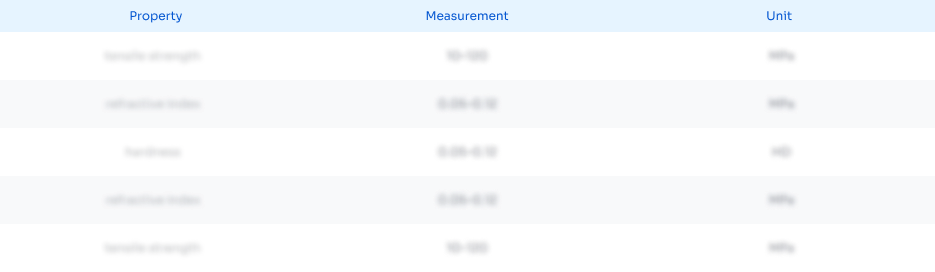
Abstract
Description
Claims
Application Information

- Generate Ideas
- Intellectual Property
- Life Sciences
- Materials
- Tech Scout
- Unparalleled Data Quality
- Higher Quality Content
- 60% Fewer Hallucinations
Browse by: Latest US Patents, China's latest patents, Technical Efficacy Thesaurus, Application Domain, Technology Topic, Popular Technical Reports.
© 2025 PatSnap. All rights reserved.Legal|Privacy policy|Modern Slavery Act Transparency Statement|Sitemap|About US| Contact US: help@patsnap.com