Textile mechanical station for manufacturing across winding reel
A cross-winding bobbin and textile machinery technology, which is applied in the direction of conveying filamentous materials, thin material processing, transportation and packaging, etc., can solve the problems of high component costs and changes, reduce power consumption, and avoid seizures Effect
- Summary
- Abstract
- Description
- Claims
- Application Information
AI Technical Summary
Problems solved by technology
Method used
Image
Examples
Embodiment Construction
[0018] FIG. 1 shows a schematic side view of a textile machine for producing cross-wound bobbins, in this embodiment a so-called automatic cross-winder. Such an automatic cross-winding winder 1 has, as is known, a number of identical work stations 2 between its end positions (not shown).
[0019] At these stations 2, bobbins 9 produced, for example, on ring spinning machines with relatively little yarn material are wound into large-volume cross-wound bobbins 11, which are then maintained by means of automatic maintenance Devices such as a cross-spool changer are transferred to a cross-wound bobbin conveyor 21 in the longitudinal direction of the machine and are conveyed to a bobbin handling station or the like arranged at the end of the machine.
[0020] According to the illustrated embodiment, some stations 2 of the automatic cross-winding machine 1 each have a bobbin magazine 3 for storing a large number of bobbins 9 .
[0021] Below the bobbin storehouse 3 that is preferab...
PUM
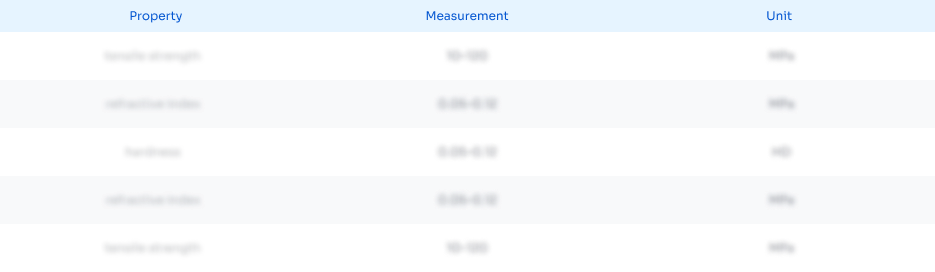
Abstract
Description
Claims
Application Information

- R&D
- Intellectual Property
- Life Sciences
- Materials
- Tech Scout
- Unparalleled Data Quality
- Higher Quality Content
- 60% Fewer Hallucinations
Browse by: Latest US Patents, China's latest patents, Technical Efficacy Thesaurus, Application Domain, Technology Topic, Popular Technical Reports.
© 2025 PatSnap. All rights reserved.Legal|Privacy policy|Modern Slavery Act Transparency Statement|Sitemap|About US| Contact US: help@patsnap.com