Manufacturing method for cross axle of universal coupling
A universal coupling and cross shaft technology, applied in the field of transmission shafting, can solve the problems of coupling jamming, short service life, small axis bending angle, etc. Effect
- Summary
- Abstract
- Description
- Claims
- Application Information
AI Technical Summary
Problems solved by technology
Method used
Examples
Embodiment Construction
[0013] specific implementation
[0014] Embodiments of the present invention are as follows:
[0015] The cross shaft of the universal joint is made of high-quality low-carbon alloy structural steel - 20CrMnTi, which is made by blanking, precision die forging, normalizing, machining, surface carburizing, surface quenching, low temperature tempering, and fine grinding. Mechanical properties; said normalizing, surface carburizing, surface quenching, and low temperature tempering process conditions are:
[0016] Normalizing: heating the steel to the critical temperature Ac 3 Above 50°C, keep warm for 8 hours, then cool with air;
[0017] Surface carburizing: the hardened surface contains 1% carbon, and the depth of carburizing layer is 0.9mm;
[0018] Surface hardening: medium frequency induction heating, frequency range: 8 kHz, hardened layer depth 6mm.
[0019] Low temperature tempering: Tempering temperature is 200℃, surface hardness is HRC60 and core hardne...
PUM
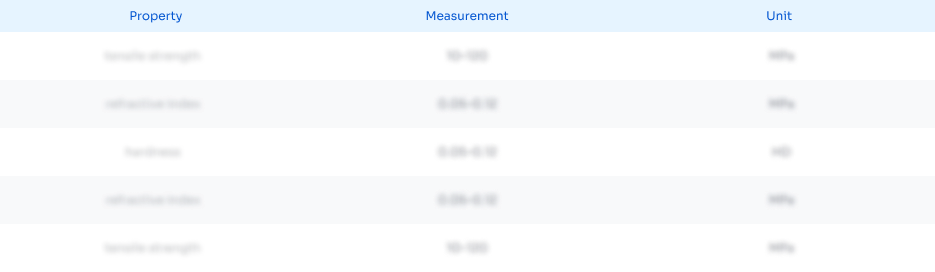
Abstract
Description
Claims
Application Information

- R&D
- Intellectual Property
- Life Sciences
- Materials
- Tech Scout
- Unparalleled Data Quality
- Higher Quality Content
- 60% Fewer Hallucinations
Browse by: Latest US Patents, China's latest patents, Technical Efficacy Thesaurus, Application Domain, Technology Topic, Popular Technical Reports.
© 2025 PatSnap. All rights reserved.Legal|Privacy policy|Modern Slavery Act Transparency Statement|Sitemap|About US| Contact US: help@patsnap.com