Toughness reinforcing phenylethylene resin composition of transparent rubber and method for preparing the same
A resin composition and a technology for toughening styrene, which are used in the field of preparation of transparent rubber toughened styrene resin compositions
- Summary
- Abstract
- Description
- Claims
- Application Information
AI Technical Summary
Problems solved by technology
Method used
Image
Examples
Embodiment 1
[0068] Preparation of core layer copolymer
[0069] Weigh 307 parts by weight of emulsifier, 1 part by weight of molecular weight modifier, 36 parts by weight of initiator solution, and 100 parts by weight of styrene monomer in a reactor, seal the reactor and add 400 parts by weight of butadiene monomer. The reaction kettle was placed in a rotary constant temperature water bath and the temperature was raised to 65°C. After 14 hours of reaction, the temperature was raised to 69°C, and the reaction was carried out for 8 hours. Then the temperature was raised to 71°C, and the reaction was continued for 4 hours. After the reaction is complete, lower the temperature and add 1 part by weight of a terminator, and discharge to obtain a core layer copolymer.
[0070] Preparation of rubbery copolymers
[0071] Inject 200 parts by weight of deionized water into a 1000ml three-necked bottle, then add 0.4 parts by weight of sodium pyrophosphate, 0.6 parts by weight of glucose and 0.01 par...
Embodiment 2
[0080] Preparation of the core layer copolymer, the components are shown in Table 1, and the same method as in Example 1 was used to obtain the core layer copolymer.
[0081] Preparation of rubber-like copolymer, the components are shown in Table 1, and the same method as in Example 1 was used to obtain the rubber-like copolymer.
[0082] Synthesis of the continuous phase of the copolymer
[0083] Take by weighing 494 parts by weight of deionized water, 3 parts by weight of hydroxymethylcellulose, and 0.1 parts by weight of sodium laurylsulfonate to prepare a suspending agent solution; 3 parts by weight of liquid paraffin, 3 parts by weight of trinonylphenyl sulfite 3 parts by weight of n-butyl mercaptan to prepare an additive solution; 7 parts by weight of 2,2'-azo-bis-2-methylbutyronitrile and 50 parts by weight of styrene monomer to prepare an initiator solution.
[0084] Add 5232 parts by weight of deionized water into the reactor, then add the prepared suspending agent s...
Embodiment 3
[0088] Preparation of the core layer copolymer, the components are shown in Table 1, and the same method as in Example 1 was used to obtain the core layer copolymer.
[0089] Preparation of rubber-like copolymer, the components are shown in Table 1, and the same method as in Example 1 was used to obtain the rubber-like copolymer.
[0090] Synthesis of the continuous phase of the copolymer
[0091] Take by weighing 494 parts by weight of deionized water, 9 parts by weight of hydroxypropyl cellulose, and 0.2 parts by weight of sodium lauryl sulfate to prepare a suspending agent solution; 300 parts by weight of styrene monomer, 6 parts by weight of liquid paraffin, trinonyl substitute 6 parts by weight of phenyl sulfite, 6 parts by weight of n-tetradecyl mercaptan to prepare an additive solution; 11 parts by weight of tert-butyl peroxyisopropyl carbonate and 100 parts by weight of styrene monomer to prepare an initiator solution.
[0092] Add 5232 parts by weight of deionized wa...
PUM
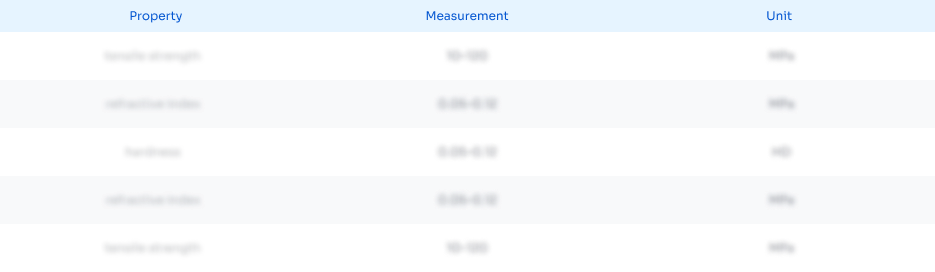
Abstract
Description
Claims
Application Information

- Generate Ideas
- Intellectual Property
- Life Sciences
- Materials
- Tech Scout
- Unparalleled Data Quality
- Higher Quality Content
- 60% Fewer Hallucinations
Browse by: Latest US Patents, China's latest patents, Technical Efficacy Thesaurus, Application Domain, Technology Topic, Popular Technical Reports.
© 2025 PatSnap. All rights reserved.Legal|Privacy policy|Modern Slavery Act Transparency Statement|Sitemap|About US| Contact US: help@patsnap.com