TiCN-base cermet and cutting tool and method for manufacturing cut article using the same
A technology for cutting tools and base metals, which is applied in the field of TiCN-based cermets, can solve the problems of low proportion of binding phase, reduced thermal shock resistance and damage resistance, and reduced strength of sintered body, so as to improve heat conduction efficiency and durability The effect of improving impact resistance and chipping resistance
- Summary
- Abstract
- Description
- Claims
- Application Information
AI Technical Summary
Problems solved by technology
Method used
Image
Examples
Embodiment
[0044] Prepare TiCN powder, TiCN-10% by mass Co doped powder, TiN powder, ZrC powder, VC powder, TaC powder, NbC powder, WC powder, Ni powder, Co powder, Ni and Co powder with the average particle size shown in Table 1. The solid solution powders of them are formulated into the composition shown in Table 1.
[0045] Next, the above formulation was wet-mixed with isopropyl alcohol using a stainless steel ball mill and ultrahard balls, and 3% by mass of paraffin was added and mixed. Then, after this mixed powder is extrusion-molded into the throw away chip (throw away chip) shape of CNMG120408 with 200MPa, carries out firing with the condition shown in Table 1 to obtain sintered compact (sample No.1 in Table 1 ~10).
[0046] In addition, regarding sample No. 5 in Table 1, as the Co and Ni source, both solid solution powder consisting of Ni: 5% by mass and Co: 6.5% by mass, and Ni powder of 5% by mass were used.
[0047] [Table 1]
[0048] sample
PUM
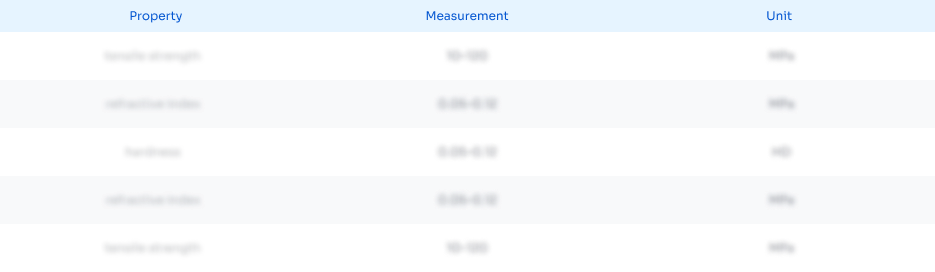
Abstract
Description
Claims
Application Information

- Generate Ideas
- Intellectual Property
- Life Sciences
- Materials
- Tech Scout
- Unparalleled Data Quality
- Higher Quality Content
- 60% Fewer Hallucinations
Browse by: Latest US Patents, China's latest patents, Technical Efficacy Thesaurus, Application Domain, Technology Topic, Popular Technical Reports.
© 2025 PatSnap. All rights reserved.Legal|Privacy policy|Modern Slavery Act Transparency Statement|Sitemap|About US| Contact US: help@patsnap.com