Terylene harness cord thread and preparing method thereof
A production method and technology of polyester, applied in the direction of textile, textile and papermaking, fiber treatment, etc., can solve problems such as the shortage of through-filament raw materials, affecting the development of jacquard fabrics or fabrics, etc., and achieve the effect of abundant raw materials, moderate price and low energy consumption
- Summary
- Abstract
- Description
- Claims
- Application Information
AI Technical Summary
Problems solved by technology
Method used
Examples
Embodiment 1
[0044] Use 20 special pure polyester yarns to twist after merging 1 share of colored yarn and 5 shares of white yarn, and control the twist to be 700 twists / meter to make polyester strands; then combine and twist the above polyester strands with 5 shares, control The twist is 300 twists / meter, and the flower-stitched polyester cable is obtained. Then the above-mentioned polyester cable is wound into a bobbin on the winding equipment, introduced into special equipment, and pulled by the rollers on the special equipment to obtain the initial traction and elongation of the polyester cable (control its elongation to be about 10%), and then The polyester cable is introduced into the dipping tank, and when passing through the dipping tank, the specially made slurry (the slurry is composed of 37 kg of epoxy resin, 37 kg of acrylic resin, 13 kg of algae powder, 8 kg of phenolic modified amine and 5 kg of water Prepared) cover and soak for 8-15 seconds, remove excess slurry when leavin...
Embodiment 2
[0046] The basic steps are the same as in Example 1, except that the polyester cable is twisted after merging 2 strands of colored yarn and 2 strands of white yarn with 30-tex pure polyester yarn, and the twist is controlled to be 600 twists / m. Polyester strands; then the above polyester strands are combined and twisted with 6 strands, and the twist is controlled to be 400 twists / m to obtain a patterned polyester cable. The slurry in the dipping tank is prepared from 38 kilograms of epoxy resin, 36 kilograms of acrylic resin, 10 kilograms of algae powder, 10 kilograms of low molecular weight polyamide and 6 kilograms of water.
Embodiment 3
[0048] The basic steps are the same as in Example 1, except that the polyester cable is twisted after merging 3 shares of colored yarn and 2 shares of white yarn with 40 special pure polyester yarn, and the twist is controlled to be 500 twists / m. Polyester strands; the above-mentioned polyester strands are combined and twisted with 4 strands, and the twist is controlled to be 200 twists / meter to obtain a patterned polyester cable. The slurry in the dipping tank is prepared from 35 kg of epoxy resin, 40 kg of acrylic resin, 15 kg of algae powder, 6 kg of phenolic modified amine and 4 kg of water.
PUM
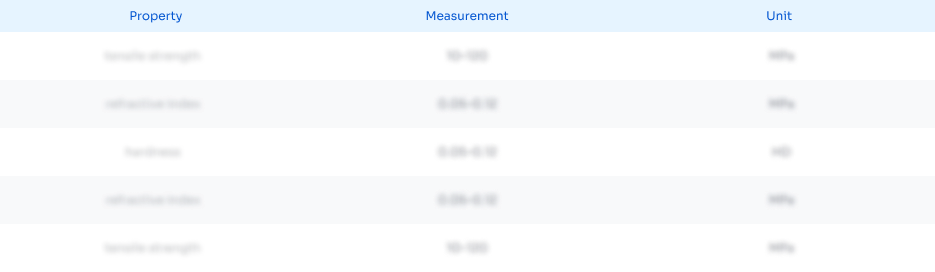
Abstract
Description
Claims
Application Information

- Generate Ideas
- Intellectual Property
- Life Sciences
- Materials
- Tech Scout
- Unparalleled Data Quality
- Higher Quality Content
- 60% Fewer Hallucinations
Browse by: Latest US Patents, China's latest patents, Technical Efficacy Thesaurus, Application Domain, Technology Topic, Popular Technical Reports.
© 2025 PatSnap. All rights reserved.Legal|Privacy policy|Modern Slavery Act Transparency Statement|Sitemap|About US| Contact US: help@patsnap.com