Coking technique using coal external burning to replace gas fuel burning
A gas fuel and process technology, applied in the field of coking process, can solve the problems of large gas consumption, high heat, low calorific value, etc., and achieve the effect of rational utilization
- Summary
- Abstract
- Description
- Claims
- Application Information
AI Technical Summary
Problems solved by technology
Method used
Image
Examples
Embodiment 1
[0033] The coking process of using external combustion of coal instead of combustion of gaseous fuels such as coke oven gas: the combustion unit in the coke production flow chart (Figure 1) is replaced by a combustion unit (Figure 2), which is a kind of external combustion of coal instead of coke oven gas combustion The new coking process flow chart. The operating conditions of the combustion unit are as follows: the pressure in the furnace is slightly positive, the temperature of the flue gas out of the furnace is 1400-1700 °C, and it is adjusted appropriately according to the heat exchange cycle. In order to compare the external combustion of coal instead of coke oven gas combustion process with the original process, using the same exhaust gas temperature of 278 °C, the heat balance data of the coke oven with an annual output of 2 million tons of coke are listed in Table 4. If the conversion efficiency of coal to gas fuel is 80%, the saved 360MNm 3 Coke oven gas is equivale...
Embodiment 2
[0036] A new type of coking process that combines external combustion of coal with combustion of gaseous fuels such as coke oven gas by combining partitioned wall heat exchange and regenerative heat exchange: a combustion unit (Figure 2), a regenerative waste heat recovery unit and a partitioned wall waste heat recovery unit (Fig. 3) Replacing the combustion unit, regenerative waste heat recovery unit and partition wall waste heat recovery unit in the coke production flow chart (Fig. 1) respectively, it is a new coking process that uses external combustion of coal instead of coke oven gas combustion picture. The operating conditions of the combustion unit are as follows: the pressure in the furnace is slightly positive, the temperature of the flue gas out of the furnace is 1400-1700 °C, and it is adjusted appropriately according to the heat exchange cycle. Waste heat recovery adopts the combination of regenerative heat exchanger and partition wall heat exchanger. The temperatu...
PUM
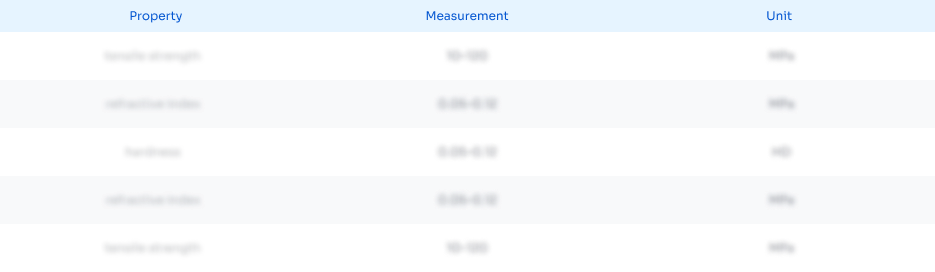
Abstract
Description
Claims
Application Information

- R&D
- Intellectual Property
- Life Sciences
- Materials
- Tech Scout
- Unparalleled Data Quality
- Higher Quality Content
- 60% Fewer Hallucinations
Browse by: Latest US Patents, China's latest patents, Technical Efficacy Thesaurus, Application Domain, Technology Topic, Popular Technical Reports.
© 2025 PatSnap. All rights reserved.Legal|Privacy policy|Modern Slavery Act Transparency Statement|Sitemap|About US| Contact US: help@patsnap.com