Porous metal vane coupling design method
A technology of porous metal and design method, which is applied to the supporting elements of blades, mechanical equipment, components of pumping devices for elastic fluids, etc. The effect of cooling air volume, improving performance and service life, and increasing specific strength
- Summary
- Abstract
- Description
- Claims
- Application Information
AI Technical Summary
Problems solved by technology
Method used
Image
Examples
Embodiment 1
[0014] Embodiment 1: The method is used in the design process of the blade of turbomachinery, which includes the following steps:
[0015] 1) Perform blade aerodynamic design;
[0016] 2) select the porosity to carry out the design of the sandwich body of the porous metal blade;
[0017] 3) Conduct strength and vibration analysis on porous metal blades;
[0018] 4) Processing the sandwich body;
[0019] 5) Process the outer lining of the blade;
[0020] 6) Check and check the porous metal blade, and repeat the above steps until the design is completed.
Embodiment 2
[0021] Embodiment 2: the method is used for the design process of fan or compressor blade, and it comprises the steps:
[0022] 1) Carry out the aerodynamic design of the fan / compressor blade, and obtain the velocity triangle, aerodynamic parameters, stage parameters and total parameters of each blade outlet along the radial section according to the overall performance requirements of the aero-engine / gas turbine; then complete the blade type Surface modeling and airfoil stacking, and finally the design results obtained through the calculation and analysis of the full three-dimensional viscous flow field are checked. If the requirements are not met, the above process is repeated until the aerodynamic performance requirements are met; Styling means to achieve advanced aerodynamic performance indicators;
[0023] 2) The fan or compressor blade that step 1) is obtained is carried out the analysis of solid metal blade intensity, according to strength analysis result, select porosit...
Embodiment 3
[0028] Embodiment 3: the method is used for the design process of turbine blade, and it comprises the steps:
[0029] 1) Carry out the aerodynamic design of the turbine blades, and obtain the velocity triangle, aerodynamic parameters, stage parameters and total parameters of each blade outlet along the radial section according to the overall performance requirements of the components of the aero-engine / gas turbine; then complete the blade surface modeling, The airfoils are stacked, and finally the design results obtained through the calculation and analysis of the full three-dimensional viscous flow field are checked. If the requirements are not met, the above process is repeated until the aerodynamic performance requirements are met; The aerodynamic performance index;
[0030] 2) Analyze the blade cooling and heat transfer characteristics of traditional metal materials for the blade obtained in step 1). According to the required blade cooling efficiency, design the porosity d...
PUM
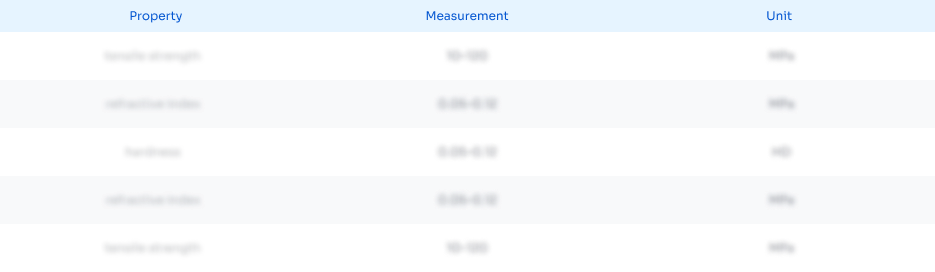
Abstract
Description
Claims
Application Information

- R&D
- Intellectual Property
- Life Sciences
- Materials
- Tech Scout
- Unparalleled Data Quality
- Higher Quality Content
- 60% Fewer Hallucinations
Browse by: Latest US Patents, China's latest patents, Technical Efficacy Thesaurus, Application Domain, Technology Topic, Popular Technical Reports.
© 2025 PatSnap. All rights reserved.Legal|Privacy policy|Modern Slavery Act Transparency Statement|Sitemap|About US| Contact US: help@patsnap.com