Method for producing naphthalenedicarboxylic acid
A manufacturing method, a technology of naphthalene dicarboxylic acid, applied in 2 fields, can solve the problems that 2,6-naphthalene dicarboxylic acid cannot have the purity of polyethylene phthalate, etc., so as to improve the purity, increase the yield, reduce the The effect of using
- Summary
- Abstract
- Description
- Claims
- Application Information
AI Technical Summary
Problems solved by technology
Method used
Image
Examples
Embodiment 1
[0052] The reactant was fed together with the catalyst into a titanium reactor with a capacity of 300 L having a condenser, a heater and a stirrer to carry out an oxidation reaction. In addition, the temperature of the oxidation reactor was adjusted to 200°C, and the pressure was adjusted to 20kg / cm 2 , rotate the stirrer at 700 rpm to disperse the reaction gas. During the reaction, add air in an amount of about 35.7 moles per 1 mole of 2,6-dimethylnaphthalene before the initial amount of recirculated gas is ensured; Naphthalene plus air was added in an amount of 22 moles. In addition, 1.8 mol of nitrogen was added as a diluent gas, and after stabilization, the circulation rate of the exhaust gas was adjusted so that the oxygen content of the exhaust gas was 4% to 6% by weight. After the crystallization step and the solid-liquid separation step after the oxidation reaction, the final product is obtained, and the final product is subjected to BSTFA displacement treatment unde...
Embodiment 2 and Embodiment 3
[0055] Production was carried out under the same conditions as in Example 1, except that the amount of acetic acid, the catalyst, and the circulation of the mother liquor were different from Example 1, thereby producing 2,6-naphthalene dicarboxylic acid. The compounds used in the reaction and the results are shown in Table 1 and Table 2, respectively.
PUM
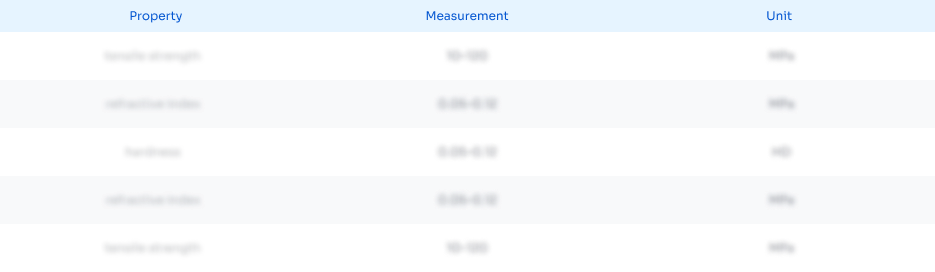
Abstract
Description
Claims
Application Information

- R&D
- Intellectual Property
- Life Sciences
- Materials
- Tech Scout
- Unparalleled Data Quality
- Higher Quality Content
- 60% Fewer Hallucinations
Browse by: Latest US Patents, China's latest patents, Technical Efficacy Thesaurus, Application Domain, Technology Topic, Popular Technical Reports.
© 2025 PatSnap. All rights reserved.Legal|Privacy policy|Modern Slavery Act Transparency Statement|Sitemap|About US| Contact US: help@patsnap.com