Electrostatic-resisting rubber board and its production
A rubber sheet, anti-static technology, applied in chemical instruments and methods, other chemical processes, etc., can solve the problems of unstable electrical properties, poor anti-static effect, low heat resistance, etc., to achieve low heat resistance, anti-static Good performance, smooth surface effect
- Summary
- Abstract
- Description
- Claims
- Application Information
AI Technical Summary
Problems solved by technology
Method used
Examples
Embodiment 1
[0026]Example 1 According to the antistatic layer components in Table 1, take the antistatic layer rubber and polyvinyl chloride resin and fuse them at a temperature of 100°C to form a rubber-plastic mixture, and combine the above-mentioned rubber-plastic mixture and antistatic The other components of the layer are internally mixed on the internal mixer, the internal mixing temperature is 100°C, and the internal mixing time is 40min; 40Min; after rubber mixing, the calender is discharged, and the antistatic layer film is made after irradiating with light intensity of 60 lux for 5 minutes; according to the components of the static conductive layer in Table 2, take the static conductive layer rubber and the static conductive layer The other components are internally mixed on the internal mixer, the internal mixing temperature is 100°C, and the internal mixing time is 40min; after internal mixing, the internal mixing is carried out on the open mixer, the initial mixing temperature...
Embodiment 2
[0032] Example 2 According to the antistatic layer components in Table 4, take the antistatic layer rubber and polyvinyl chloride resin and fuse them at a temperature of 150°C to form a rubber-plastic mixture. The above-mentioned rubber-plastic mixture and antistatic The other components of the layer are internally mixed on the internal mixer, the internal mixing temperature is 110°C, and the internal mixing time is 37min; 37Min; After rubber mixing, the calender is discharged and the antistatic layer film is made after being irradiated with light of 80 lux light intensity for 4 minutes; according to the static conductive layer components in Table 5, take the static conductive layer rubber and the static conductive layer The other components are internally mixed on the internal mixer, the internal mixing temperature is 110°C, and the internal mixing time is 37min; after internal mixing, the internal mixing is carried out on the open mixer, the initial mixing temperature is 80°C...
Embodiment 3
[0038] Example 3 According to the antistatic layer components in Table 7, take the antistatic layer rubber and polyvinyl chloride resin and fuse them at a temperature of 180°C to form a rubber-plastic mixture. The above-mentioned rubber-plastic mixture and antistatic The other components of the layer are internally mixed on the internal mixer, the internal mixing temperature is 130°C, and the internal mixing time is 35min; 35Min; after rubber mixing, the calender is discharged and then irradiated with light of 120 lux intensity for 3 minutes to make an antistatic layer film; according to the static conductive layer components in Table 8, take the static conductive layer rubber and the static conductive layer The other components are internally mixed on the internal mixer, the internal mixing temperature is 130°C, and the internal mixing time is 35min; after internal mixing, the internal mixing is carried out on the open mixer, the initial mixing temperature is 90°C, and the int...
PUM
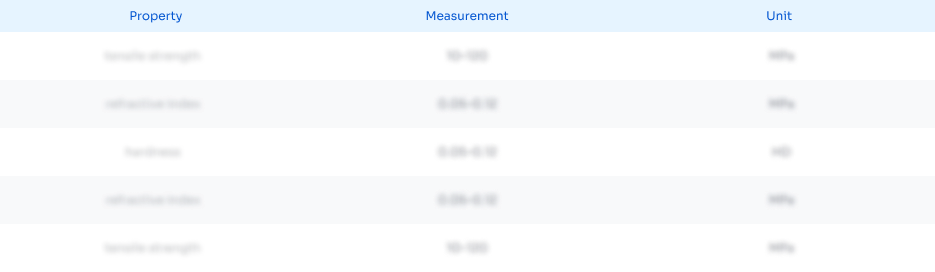
Abstract
Description
Claims
Application Information

- R&D
- Intellectual Property
- Life Sciences
- Materials
- Tech Scout
- Unparalleled Data Quality
- Higher Quality Content
- 60% Fewer Hallucinations
Browse by: Latest US Patents, China's latest patents, Technical Efficacy Thesaurus, Application Domain, Technology Topic, Popular Technical Reports.
© 2025 PatSnap. All rights reserved.Legal|Privacy policy|Modern Slavery Act Transparency Statement|Sitemap|About US| Contact US: help@patsnap.com