Method for preparing solar-grade silicon material by melt-salt electrolysis method
A solar and molten salt technology, applied in the electrolysis process, electrolysis components, polycrystalline material growth and other directions, can solve the problems of equipment corrosion, no impurity removal, and low efficiency.
- Summary
- Abstract
- Description
- Claims
- Application Information
AI Technical Summary
Problems solved by technology
Method used
Examples
Embodiment 1
[0011] SiO with a purity of 99.46% 2 As raw material, its impurity content is Na 1000ppm, K 240ppm, Mg66ppm, Ca 490ppm, Fe 2000ppm, B 120ppm, Cu 20ppm, Ti 73ppm, Mn 200ppm, Ni 53ppm, other 52ppm; high-purity metal Cu is the cathode, and high-purity graphite is Anode with electrolyte composition of 48% Na 3 AlF 6 -32%AlF 3 -20%Na 2 SiF 6 , electrolysis temperature 850℃, current density 0.5A / cm 2 The silicon-containing alloy Si-Cu is electrolytically prepared under the conditions, and the silicon content is 15%.
[0012] The obtained silicon-containing alloy Si-Cu is used as the anode, the high-purity metal Al is used as the cathode, and the electrolyte composition is 70% K 3 AlF 6 -7%AlF 3 -15%BaF 2 -8%K 2 SiF 6 , electrolysis temperature 950℃, current density 0.5A / cm 2 The high-purity silicon-containing alloy Si-Al is electrolytically prepared under the conditions, and the silicon content is 40%.
[0013] Using high-purity silicon-containing alloy Si-Al as raw mat...
Embodiment 2
[0015] With a purity of 99.44% K 2 SiF 6 As a raw material, its impurity content is 0.5% of free acid (calculated as fluosilicic acid), 0.02% of fluoride, 0.02% of sulfate, 0.01% of iron, and 0.01% of heavy metal; high-purity metal Cu is the cathode, and high-purity graphite is the anode. Electrolyte composition 72.5% K 3 AlF 6 -10.5%AlF 3 -12%K 2 SiF 6 -5%CaF 2 , electrolysis temperature 900℃, current density 0.75A / cm 2The silicon-containing alloy Si-Cu is electrolytically prepared under the conditions, and the silicon content is 18%.
[0016] The obtained silicon-containing alloy Si-Cu is used as the anode, the high-purity metal Ca is used as the cathode, and the electrolyte composition is 67.5% K 3 AlF 6 -7.5%AlF 3 -8%K 2 SiF 6 -5%CaF 2 -12%BaF 2 , electrolysis temperature 920℃, current density 0.8A / cm 2 The high-purity silicon-containing alloy Si-Ca is electrolytically prepared under the conditions, and the silicon content is 6%.
[0017] Using high-purity ...
Embodiment 3
[0019] With 99.5% SiO 2 As raw material, its impurity content is Na 1120ppm, K 278ppm, Mg 75ppm, Ca 543ppm, Fe 2467ppm, B 136ppm, Cu 33ppm, Ti 78ppm, Mn 169ppm, Ni58ppm, other 43ppm; high-purity metal Zn is the cathode, and high-purity graphite is Anode with electrolyte composition of 69.5% Na 3 AlF 6 -6%AlF 3 -20%Na 2 SiF 6 -4.5%CaF 2 , electrolysis temperature 970℃, current density 0.5A / cm 2 The silicon-containing alloy Si-Zn is electrolytically prepared under the conditions, and the silicon content is 13%.
[0020] The obtained silicon-containing alloy Si-Zn is used as the anode, high-purity graphite is used as the cathode, and the electrolyte composition is 72% Na 3 AlF 6 -15%BaF 2 -5%CaF 2 -8%K 2 SiF 6 , electrolysis temperature 1425℃, current density 0.5A / cm 2 Electrolytic preparation under the conditions to obtain solar-grade polysilicon materials. Its purity is 99.999924%, including 0.03ppm iron, 0.027ppm aluminum, 0.063ppm calcium, 0.18ppm phosphorus, 0....
PUM
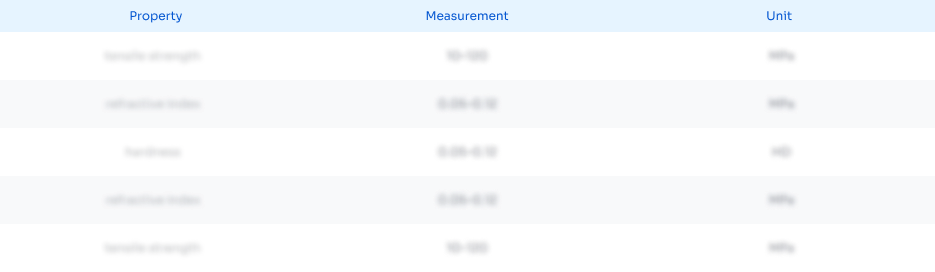
Abstract
Description
Claims
Application Information

- Generate Ideas
- Intellectual Property
- Life Sciences
- Materials
- Tech Scout
- Unparalleled Data Quality
- Higher Quality Content
- 60% Fewer Hallucinations
Browse by: Latest US Patents, China's latest patents, Technical Efficacy Thesaurus, Application Domain, Technology Topic, Popular Technical Reports.
© 2025 PatSnap. All rights reserved.Legal|Privacy policy|Modern Slavery Act Transparency Statement|Sitemap|About US| Contact US: help@patsnap.com