Bars and tubes material unsymmetrical radial welding punched high performance precision blanking method
A precision blanking, asymmetric technology, applied in metal processing equipment, hammer driving devices, etc., can solve the problem of limited material range, and achieve the effect of wide processing range, high efficiency and good quality
- Summary
- Abstract
- Description
- Claims
- Application Information
AI Technical Summary
Problems solved by technology
Method used
Image
Examples
Embodiment Construction
[0017] The asymmetrical radial forging precision blanking method of the rod and tube material of the present invention utilizes the fatigue fracture mechanism of the rod and tube material, and cyclically loads the rod and tube material by depressing the radial direction of the rod and tube material by the hammer head. The working contour curve of the hammer head adopts a cycloid, which can perform radial sliding movement under the constraint of the radial sliding groove. In order to realize the radial feed movement of the hammer head, a cylindrical cam is used to cooperate with it. The cylindrical cam can rotate freely around its central axis, and the relative motion between the hammer head and the cylindrical cam is rolling friction. The rod and tube material is fixed and still, using 4 uniformly arranged hammerheads, which are constantly in contact with 7 cylindrical cams distributed along the circumference, so that the load is continuously applied in the radial direction, wh...
PUM
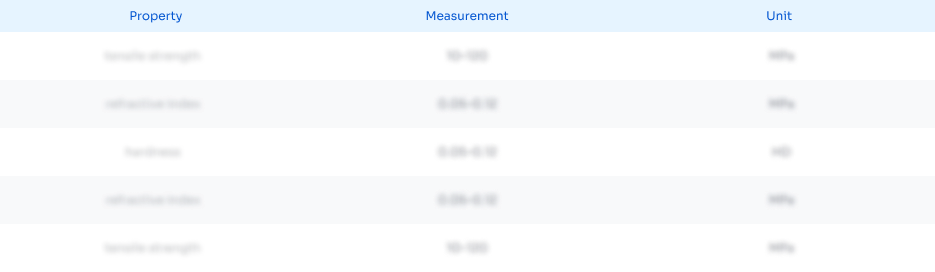
Abstract
Description
Claims
Application Information

- R&D
- Intellectual Property
- Life Sciences
- Materials
- Tech Scout
- Unparalleled Data Quality
- Higher Quality Content
- 60% Fewer Hallucinations
Browse by: Latest US Patents, China's latest patents, Technical Efficacy Thesaurus, Application Domain, Technology Topic, Popular Technical Reports.
© 2025 PatSnap. All rights reserved.Legal|Privacy policy|Modern Slavery Act Transparency Statement|Sitemap|About US| Contact US: help@patsnap.com