Hybrid construction machine
A construction machinery and hybrid technology, applied in hybrid vehicles, construction, machinery and equipment, etc., can solve problems such as reduced operating performance and inability to achieve, achieve poor operability, restrain power consumption, and prevent abnormal decline or excessive. The effect of discharge
- Summary
- Abstract
- Description
- Claims
- Application Information
AI Technical Summary
Problems solved by technology
Method used
Image
Examples
no. 1 Embodiment approach
[0034] 1st Embodiment (refer FIG. 1-FIG. 4)
[0035]FIG. 1 shows a block diagram of a hybrid excavator according to an embodiment. As shown in the figure, a hydraulic pump 12 and a generator motor 13 functioning as a generator and a motor are connected in parallel to the engine 10 via a power splitter 11 . The hydraulic pump 12 and the generator motor 13 are driven by the engine 10 . A plurality of hydraulic actuators are connected to the hydraulic pump 12 via a control valve 14 . The control valve 14 in FIG. 1 represents an aggregate of a plurality of control valves. The actual control valve 14 is provided corresponding to each hydraulic actuator. The plurality of actuators are the respective pressure cylinders 7 , 8 , and 9 of the boom, the arm, and the bucket shown in FIG. 8 , and the left and right travel motors 15 , 16 . The respective hydraulic actuators 7 , 8 , 9 , 15 , 16 are driven by pressure oil supplied from a hydraulic pump 12 . In addition, although the case...
no. 2 Embodiment approach
[0053] 2nd Embodiment (refer FIG. 5, FIG. 6)
[0054] The configuration block diagram of the second embodiment is the same as that of the first embodiment, so illustration is omitted.
[0055] 5 and 6 are flowcharts for explaining the operation of the second embodiment. Steps S11 to S15 in FIG. 5 are the same as steps S1 to S5 in FIG. 2 . In the second embodiment, step S16 and step S17 are provided in parallel with the procedures of steps S11 to S15. In step S16 , a pump tilt calculation value qtmp (cc / rev) based on normal control is calculated from the hydraulic actuator operation signal, the pump pressure, and the like (corresponding to step S9 in FIG. 3 ). In addition, in step S17, the speed command value Ns based on the normal control is calculated from the rotation operation signal and the like.
[0056] Thereafter, in step S18 of FIG. 6 , the ratio of the sum of the operation amounts of the hydraulic actuators to the operation amount of the rotary electric motor 18 is...
no. 3 Embodiment approach
[0059] 3rd Embodiment (refer FIG. 7)
[0060]In the third embodiment, the pump maximum output and the rotary electric motor maximum output are determined not by the operation amount but by the operation mode. Differences from the second embodiment will be described using FIGS. 5 and 6 .
[0061] After steps S11 to S17 in FIG. 5 , in a step equivalent to step S18 in FIG. 6 , according to the preset pump output power ratio Rp and rotation The motor output power ratio Rs determines the maximum output of the pump and the maximum output of the rotary motor.
[0062] For example, in operation mode 9 in FIG. 7 , when boom operation, stick operation, and swing operation are simultaneously performed, the pump output power ratio Rp is 67% (2 / 3), and the swing motor output power ratio Rs is 33% ( 1 / 3). The total power supply Pmax is divided into pump output and rotary motor output in this ratio.
[0063] The third embodiment focuses on determining the operation mode according to the ...
PUM
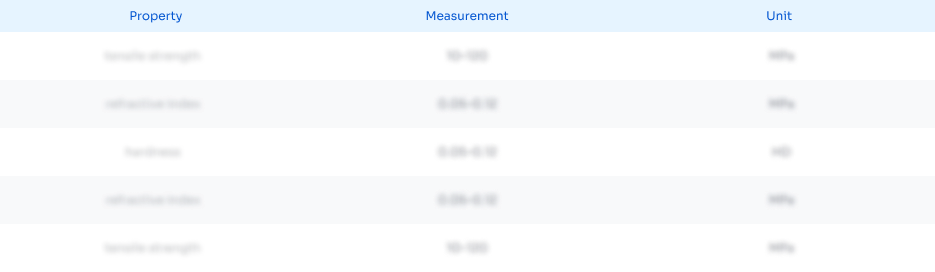
Abstract
Description
Claims
Application Information

- R&D
- Intellectual Property
- Life Sciences
- Materials
- Tech Scout
- Unparalleled Data Quality
- Higher Quality Content
- 60% Fewer Hallucinations
Browse by: Latest US Patents, China's latest patents, Technical Efficacy Thesaurus, Application Domain, Technology Topic, Popular Technical Reports.
© 2025 PatSnap. All rights reserved.Legal|Privacy policy|Modern Slavery Act Transparency Statement|Sitemap|About US| Contact US: help@patsnap.com