Production of aqueous-dispersing alkyd resin
A technology of alkyd resin and dispersibility, applied in the chemical industry, can solve the problems of alkyd resin coating water resistance, etc., and achieve the effect of high hardness, high product purity and simple process
- Summary
- Abstract
- Description
- Claims
- Application Information
AI Technical Summary
Problems solved by technology
Method used
Examples
Embodiment 1
[0032] Add 29g of dehydrated castor oil and 25g of trimethylolpropane into the four-necked flask, and raise the temperature to 180°C under nitrogen protection and condensing and reflux conditions. When the solid reactants are completely melted, start stirring. During this process, 0.005 g of lithium hydroxide was added to facilitate the transesterification reaction. Keep the reaction temperature for 1 hour, add 24g of phthalic anhydride, and raise the temperature to 220°C for esterification. In the later stage of 3h, it was carried out under reduced pressure, and the vacuum degree was maintained at about 10132.5 Pa (0.1 atmospheric pressure). Measure system acid value during this period, when system acid value is lower than 8mgKOH / g, stop this step reaction. Lower the temperature of the reaction system to 190°C, add 6.3g of trimellitic anhydride, measure the acid value of the system after 1 hour of reaction, when the acid value reaches between 40mg KOH / g and 60mg KOH / g, lower...
Embodiment 2
[0034] According to the formula of Example 2 in Table 1, adopt the same method of Example 1 to prepare water-dispersible alkyd resin. The transesterification reaction temperature of dehydrated castor oil and trimethylolpropane is 190° C., and the time is 2 hours. The esterification temperature after adding phthalic anhydride was 240°C, and the temperature when trimellitic anhydride was added was 190°C. The temperature at the time of adding ethylene glycol butyl ether and triethylamine was 120°C.
[0035] The properties of the obtained resin and paint film are shown in Example 2 of Table 2.
Embodiment 3
[0037] According to the formula of example 3 in table 1, adopt the same method of embodiment 1 to prepare water-dispersible alkyd resin. The temperature of the transesterification reaction between dehydrated castor oil and trimethylolpropane is 200° C., and the time is 1 h. The esterification temperature after adding phthalic anhydride was 220°C, and the temperature when trimellitic anhydride was added was 200°C. The temperature at the time of adding ethylene glycol butyl ether and triethylamine was 140°C.
[0038] The properties of the obtained resin and paint film are shown in Example 3 of Table 2.
PUM
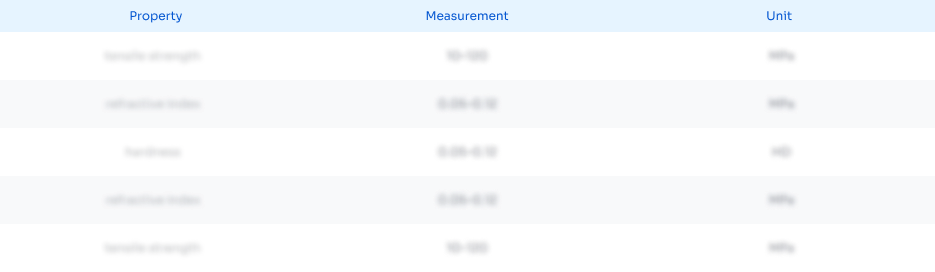
Abstract
Description
Claims
Application Information

- R&D Engineer
- R&D Manager
- IP Professional
- Industry Leading Data Capabilities
- Powerful AI technology
- Patent DNA Extraction
Browse by: Latest US Patents, China's latest patents, Technical Efficacy Thesaurus, Application Domain, Technology Topic, Popular Technical Reports.
© 2024 PatSnap. All rights reserved.Legal|Privacy policy|Modern Slavery Act Transparency Statement|Sitemap|About US| Contact US: help@patsnap.com