Method for making self-temperature-regulating phase-change heat-insulation wall and product thereof
A composite thermal insulation and manufacturing method technology, applied in chemical instruments and methods, building structure, solid waste management, etc., can solve the problems of poor fireproof performance, cracking of plastering mortar, high construction cost, etc., and achieve high thermal insulation effect, The effect of the ability to raise the indoor temperature
- Summary
- Abstract
- Description
- Claims
- Application Information
AI Technical Summary
Problems solved by technology
Method used
Image
Examples
Embodiment 1
[0069] A method for manufacturing a self-regulating phase-change composite thermal insulation wall, comprising scraping and coating self-regulating phase-change mortar on the outside of the wall, scraping and coating thermal insulation putty on the outside of the self-regulating phase-change mortar, and then scraping and coating the outside of the wall Elastomeric putty, apply a sealer primer, and finally apply an insulating paint over it.
[0070] Said self-regulating phase-change mortar is composed of the following components according to weight percentage:
[0071] Self-regulating phase change material 10%;
[0072] Hollow fiber material 15%;
[0073] Dispersible rubber powder 18%;
[0074] Cement 22%;
[0075] Light aggregate 35%.
[0076] Put the above-mentioned self-regulating phase change material, hollow fiber material and lightweight aggregate in the first mixing tank and stir and disperse for 20-30 minutes as the first component, and put the dispersible rubber po...
Embodiment 2
[0095] A method for manufacturing a self-regulating phase-change composite thermal insulation wall, comprising scraping and coating self-regulating phase-change mortar on the outside of the wall, scraping and coating thermal insulation putty on the outside of the self-regulating phase-change mortar, and then scraping and coating the outside of the wall Elastomeric putty, apply a sealer primer, and finally apply an insulating paint over it.
[0096] In the above technical solution, the thermal insulation putty is composed of the following components in percentage by weight:
[0097] Rubber powder 18%;
[0098] Cement 16%;
[0099] Light aggregate 35%;
[0100] Fiber 13%;
[0101] Expanded glass microspheres 18%;
[0102] Said fibers are a mixture of inorganic fibers and organic fibers;
[0103] The said lightweight aggregate mainly includes diatomite, floating beads, ceramsite, fly ash, expanded vitrified microspheres, hollow glass beads and perlite, or a mixture of two or...
Embodiment 3
[0106] A method for manufacturing a self-regulating phase-change composite thermal insulation wall, comprising scraping and coating self-regulating phase-change mortar on the outside of the wall, scraping and coating thermal insulation putty on the outside of the self-regulating phase-change mortar, and then scraping and coating the outside of the wall Elastomeric putty, apply a sealer primer, and finally apply an insulating paint over it.
[0107] In the above technical scheme, said elastic putty is composed of the following components according to weight percentage:
[0108] Elastic Lotion 12%;
[0109] Synthetic rubber powder 12%;
[0110] Quartz powder 23%;
[0112] Talc 13%;
[0113] Water 27%.
[0114] Put the above-mentioned synthetic rubber powder, quartz powder, calcium carbonate, talcum powder and water together and fully stir for 20-36 minutes. After uniformity, add elastic emulsion and stir slowly to form a paste.
PUM
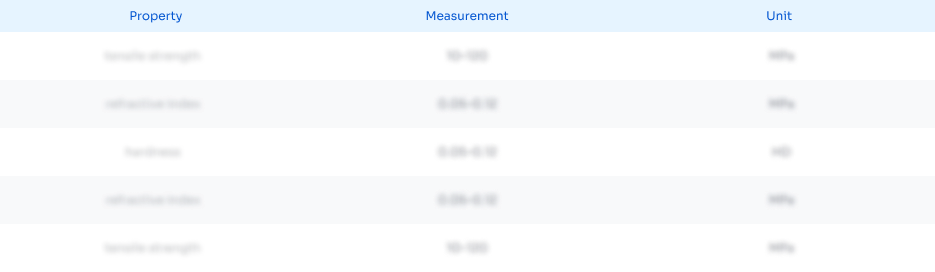
Abstract
Description
Claims
Application Information

- R&D
- Intellectual Property
- Life Sciences
- Materials
- Tech Scout
- Unparalleled Data Quality
- Higher Quality Content
- 60% Fewer Hallucinations
Browse by: Latest US Patents, China's latest patents, Technical Efficacy Thesaurus, Application Domain, Technology Topic, Popular Technical Reports.
© 2025 PatSnap. All rights reserved.Legal|Privacy policy|Modern Slavery Act Transparency Statement|Sitemap|About US| Contact US: help@patsnap.com