Methods of measuring and compensating cutting size on chamfering machine of sheet material
A technology of chamfering device and measuring method, which is applied in the direction of automatic control device, metal processing equipment, measuring/indicating equipment, etc., can solve the problems of increasing equipment burden or work burden, time-consuming, error increase, etc., and achieve the reduction of measurement costs Effect of time required and workload
- Summary
- Abstract
- Description
- Claims
- Application Information
AI Technical Summary
Problems solved by technology
Method used
Image
Examples
Embodiment Construction
[0031] Hereinafter, embodiments of the present invention will be described with reference to the drawings. As shown in FIG. 7 , on the chamfering device implementing the method of the present invention, there are lower cameras 6 , 6 for reading the chamfering lines of the lower surfaces of opposite edges of the processed plate 1 . The workbench 2, the tool 3, the camera (upper camera) 5 for reading the positioning mark, and the installation structure of these parts and the positioning mark 4 provided on the board 1 are all the same as conventional ones. The upper and lower cameras 5, 6 and the tool 3 are loaded on the same supporting platform (not shown in the figure), and can move freely along the width direction respectively, and the positional relationship between the tool 3 and the cameras 5, 6 in the feeding direction remains unchanged . The lower cameras 6, 6 move to the position directly below the upper cameras 5, 5 only when reading the processing size described later...
PUM
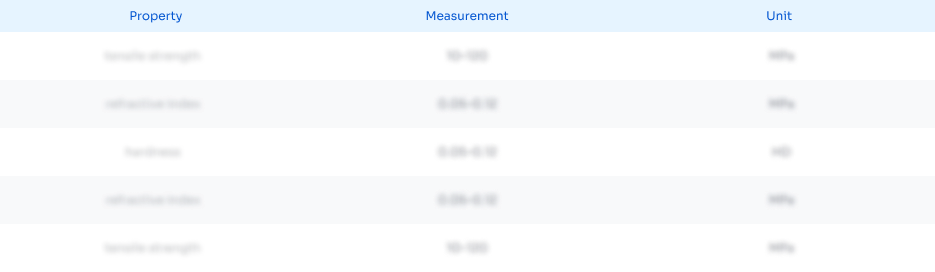
Abstract
Description
Claims
Application Information

- Generate Ideas
- Intellectual Property
- Life Sciences
- Materials
- Tech Scout
- Unparalleled Data Quality
- Higher Quality Content
- 60% Fewer Hallucinations
Browse by: Latest US Patents, China's latest patents, Technical Efficacy Thesaurus, Application Domain, Technology Topic, Popular Technical Reports.
© 2025 PatSnap. All rights reserved.Legal|Privacy policy|Modern Slavery Act Transparency Statement|Sitemap|About US| Contact US: help@patsnap.com