Reproduction and utilization method of powder generated in mechanically processing sintered Nd-Fe-B permanent magnet
A technology of mechanical processing and processing method, which is applied in the processing field of recycling and recycling of powder chips generated after sintered NdFeB permanent magnets are mechanically processed, and achieves the effects of less investment, simple equipment and facilities, and low value
- Summary
- Abstract
- Description
- Claims
- Application Information
AI Technical Summary
Problems solved by technology
Method used
Examples
Embodiment 1
[0020] The treatment method for the recycling of powder chips produced after machining of sintered NdFeB permanent magnets: the NdFeB powder chips formed after machining and other sundries attached to the processing process are mixed together and collected together; firstly, use The method of magnetic separation removes the impurities, and the NdFeB powder containing water and oil is separated from it; then the sorted NdFeB powder containing water and oil is baked in a vacuum oven: baking Baking should be carried out under a vacuum condition of not less than 1Pa. After the vacuum condition is reached, first keep warm at 30°C-35°C (30°C, 31°C, 32°C, 33°C, 34°C, 35°C) to make the NdFeB powder Shave and dry to a semi-dry state, and then bake at 60°C-65°C (60°C, 61°C, 62°C, 63°C, 64°C, 65°C) until completely dry, so that completely dry NdFeB powder can be obtained (purity above 99.9%);
[0021]When making NdFeB300 / 110 brand sintered NdFeB permanent magnets, firstly carry out batc...
Embodiment 2
[0026] The treatment method for obtaining the regenerated NdFeB powder is the same as that of Example 1.
[0027] When making NdFeB280 / 135 brand sintered NdFeB permanent magnets, firstly carry out batching, smelting, and make 215 kg of coarse powder according to the usual process, and then use 90 kg of coarse powder to prepare fine powder according to the usual process (at this time, the oxygen intake is 90ppm- 120ppm). Add 7.5 kg of the regenerated NdFeB powder to the remaining 125 kg of normal coarse powder to produce a fine powder, but when the fine powder is made, the oxygen intake is lowered to 20ppm-50ppm, and then the regenerated NdFeB powder is added and the two fine powders added with regenerated NdFeB powder were mixed and formed separately, and then the two materials were sintered and tempered together in the same sintering furnace to produce a blank. After testing the magnetic properties, the magnet with regenerated NdFeB powder was compared with that without Comp...
Embodiment 3
[0032] The treatment method for obtaining the regenerated NdFeB powder is the same as that of Example 1.
[0033] When making NdFeB280 / 96 brand sintered NdFeB permanent magnets, first carry out batching, smelting, and make 192 kg of coarse powder according to the usual process, and then use 100 kg of coarse powder to prepare fine powder according to the usual process, (the amount of oxygen input at this time is 90ppm -120ppm), mixing, and then the remaining 92 kilograms of coarse powder are produced into fine powder, but the amount of oxygen input is lowered to 20ppm-50ppm when fine powder is made, and the regenerated NdFeB powder is mixed before it is made into fine powder Add 7.4 kg to mix the materials together, and then shape the two fine powders without adding recycled NdFeB powder and adding recycled NdFeB powder separately, and then sinter and temper the two materials together in the same sintering furnace to produce a blank. After testing Magnetic properties, compared ...
PUM
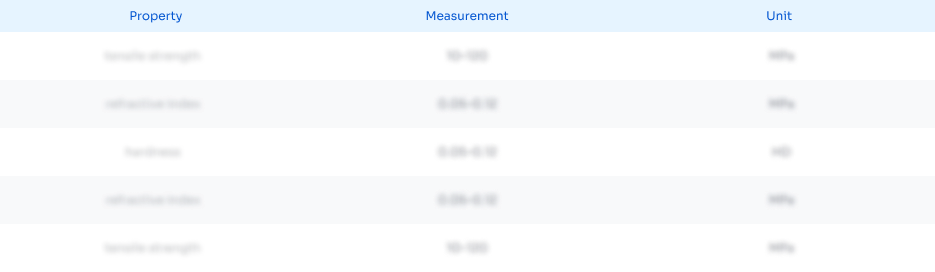
Abstract
Description
Claims
Application Information

- R&D
- Intellectual Property
- Life Sciences
- Materials
- Tech Scout
- Unparalleled Data Quality
- Higher Quality Content
- 60% Fewer Hallucinations
Browse by: Latest US Patents, China's latest patents, Technical Efficacy Thesaurus, Application Domain, Technology Topic, Popular Technical Reports.
© 2025 PatSnap. All rights reserved.Legal|Privacy policy|Modern Slavery Act Transparency Statement|Sitemap|About US| Contact US: help@patsnap.com