Device for implementing shaping high power caser diode pile light beam
A laser diode and beam shaping technology, which is applied in the application field of laser technology to achieve the effect of eliminating dark areas and improving beam quality
- Summary
- Abstract
- Description
- Claims
- Application Information
AI Technical Summary
Problems solved by technology
Method used
Image
Examples
Embodiment Construction
[0021] This embodiment will be described in detail below with reference to FIGS. 1 to 4 .
[0022] As shown in Figure 1, the laser diode stack is composed of 5 bars. After collimating the fast axis, the spot size 1 of each bar is about 10mm*0.8mm, that is, d5=10mm, d2=0.8mm, fast, The slow axis optical parameter product is about 2mm.mrad, 500mm.mrad. The thickness of the heat sink between the bars of the laser diode stack is d1=1.8mm, then the product of the fast and slow axis optical parameters of the laser diode stack is about 22mm.mrad and 500mm.mrad. The width d5 along the slow axis direction of the stacked step mirror 2 and the height d6 along the fast axis direction are the same as the laser diode stack spot, ie d5=10mm, d6=5d2+4d1=11.2mm. The 6 reflectors in each row are staggered back and forth along the light transmission direction Z2, and the distance is equal to the sum of the spot sizes in the fast axis direction of the laser diode stack, that is, d3=5d2=4mm, an...
PUM
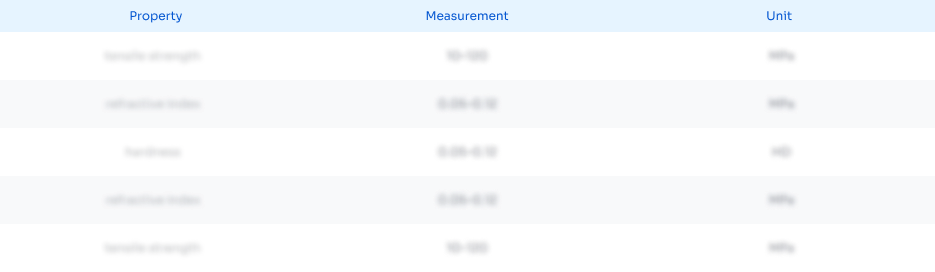
Abstract
Description
Claims
Application Information

- R&D
- Intellectual Property
- Life Sciences
- Materials
- Tech Scout
- Unparalleled Data Quality
- Higher Quality Content
- 60% Fewer Hallucinations
Browse by: Latest US Patents, China's latest patents, Technical Efficacy Thesaurus, Application Domain, Technology Topic, Popular Technical Reports.
© 2025 PatSnap. All rights reserved.Legal|Privacy policy|Modern Slavery Act Transparency Statement|Sitemap|About US| Contact US: help@patsnap.com