Plane wheel space displacement measuring system of landing gear lowering shock test
A technology of spatial displacement and measurement system, applied in measurement devices, instruments, etc., can solve problems such as installation difficulties
- Summary
- Abstract
- Description
- Claims
- Application Information
AI Technical Summary
Problems solved by technology
Method used
Image
Examples
Embodiment Construction
[0012] As shown in Figure 1, the present invention is made up of space positioning manipulator 1, angle sensor 2, bearing 3, magnetic attraction element 4 and 5 and computer 7, and three space positioning manipulator 1 is the form of series hinge, three articulated The shafts are all rotation angle sensors 2, and the fourth rotation angle sensor 2 is installed vertically on the top of the support 3. The upper end of the rotation axis is hinged with the lower end of the third space manipulator 1 connected in series. The computer 7 is connected, the magnetic attraction element 4 is connected with the free end of the mechanical arm 1 , and the magnetic attraction element 5 is fixed on the aircraft wheel 8 .
[0013] As shown in FIG. 2 , the magnetic attraction element 4 is a concave curved surface structure, the magnetic attraction element 5 is a convex curved surface structure, and the magnetic attraction elements 4 and 5 are strong magnetic attraction elements of NdFeB. In orde...
PUM
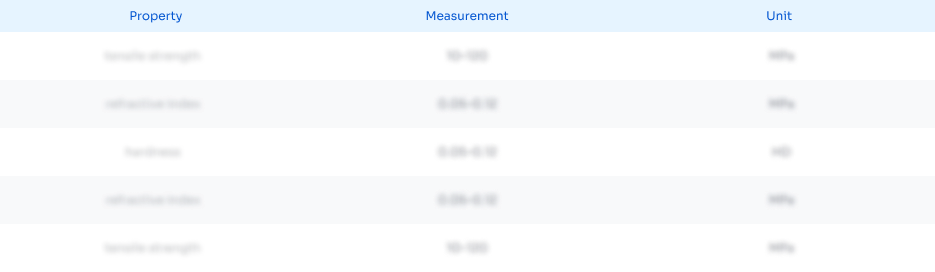
Abstract
Description
Claims
Application Information

- R&D Engineer
- R&D Manager
- IP Professional
- Industry Leading Data Capabilities
- Powerful AI technology
- Patent DNA Extraction
Browse by: Latest US Patents, China's latest patents, Technical Efficacy Thesaurus, Application Domain, Technology Topic, Popular Technical Reports.
© 2024 PatSnap. All rights reserved.Legal|Privacy policy|Modern Slavery Act Transparency Statement|Sitemap|About US| Contact US: help@patsnap.com