One-step molding technique of carbon stirrup and used stirrup-molding mould thereof
A forming process and forming die technology, applied in metal processing equipment and other directions, can solve the problems of unguaranteed product quality, low production efficiency, unable to meet the needs of economic development, etc., and achieve stable performance, high forming quality, and high batch efficiency. produce good results
- Summary
- Abstract
- Description
- Claims
- Application Information
AI Technical Summary
Problems solved by technology
Method used
Image
Examples
Embodiment Construction
[0031] The implementation of the one-time forming process of the carbon-based clamp and the clamp forming tool set used in the present invention will be described in detail below with reference to the accompanying drawings of the embodiment.
[0032] Figure 1a It is a schematic diagram of the clamp forming knife used in the primary forming process of the carbon clamp of the present invention.
[0033] Figure 1b for Figure 1a Left view of the schematic diagram of the clamp forming knife.
[0034] figure 2 It is a schematic flow chart of the one-time forming process of the carbon clamp of the present invention.
[0035] Figure 3a It is a schematic diagram of a carbon clamp formed by the process of the present invention.
[0036] Figure 3b for Figure 3a Left view of the clamp formed in .
[0037] The flow of the one-time forming process of the carbon-based clamp of the present invention will be described in detail below.
[0038] The one-time forming process of the...
PUM
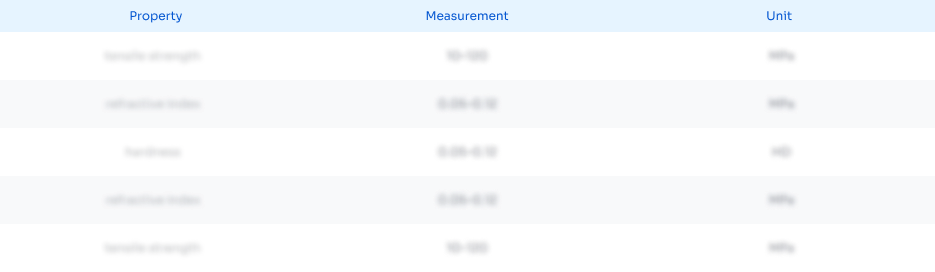
Abstract
Description
Claims
Application Information

- R&D Engineer
- R&D Manager
- IP Professional
- Industry Leading Data Capabilities
- Powerful AI technology
- Patent DNA Extraction
Browse by: Latest US Patents, China's latest patents, Technical Efficacy Thesaurus, Application Domain, Technology Topic, Popular Technical Reports.
© 2024 PatSnap. All rights reserved.Legal|Privacy policy|Modern Slavery Act Transparency Statement|Sitemap|About US| Contact US: help@patsnap.com