Dart carded felt guillotine
A cutting machine and felt technology, which is used in the cutting of textile materials, textiles and papermaking, metal processing, etc., can solve the problems of the incision quality of needle punched felt cannot be guaranteed, the service life of the hob is short, and it is fragile and felt. Achieve excellent self-cooling effect, ensure production efficiency, and save the effect of cumbersome work
- Summary
- Abstract
- Description
- Claims
- Application Information
AI Technical Summary
Problems solved by technology
Method used
Image
Examples
Embodiment Construction
[0021] please see figure 1 , according to the common sense known in the industry, the needle felt cutting mechanism of the present invention is equipped next to the needle felt forming processor at the needle felt production site, and enters into the needle felt forming processor after the needle punching is completed. Processing, the thickness after processing is usually fed to the cutting table 1 of the present invention at the felt 4 of 0.4-0.8cm, on the cutting table 1, a hob groove 11 is preset, as shown in the figure, the hob groove 11 is provided In the width direction of the cutting table 1, and offset to one end (exit end) of the cutting table 1.
[0022] The traction motor 31 of the traction mechanism 3 is a positive and negative motor, which is installed and fixed on one end of the guide rail 32, that is, installed on the right end of the current illustrated position state, and the cross-section shape is preferably two sides of the guide rail 32 of I-shape. Each en...
PUM
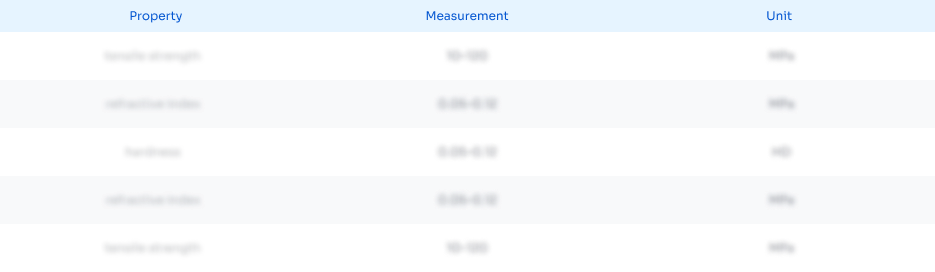
Abstract
Description
Claims
Application Information

- R&D
- Intellectual Property
- Life Sciences
- Materials
- Tech Scout
- Unparalleled Data Quality
- Higher Quality Content
- 60% Fewer Hallucinations
Browse by: Latest US Patents, China's latest patents, Technical Efficacy Thesaurus, Application Domain, Technology Topic, Popular Technical Reports.
© 2025 PatSnap. All rights reserved.Legal|Privacy policy|Modern Slavery Act Transparency Statement|Sitemap|About US| Contact US: help@patsnap.com