Magnetostrictive displacement sensor
A displacement sensor and magnetostrictive technology, applied in the field of displacement sensors, can solve problems such as narrow linear range, low frequency response of differential inductance, and large temperature influence, so as to improve anti-interference and stability, reduce Power consumption and cost, the effect of enhancing the anti-interference ability
- Summary
- Abstract
- Description
- Claims
- Application Information
AI Technical Summary
Problems solved by technology
Method used
Image
Examples
Embodiment Construction
[0020] The present invention will be further described in detail below in conjunction with the accompanying drawings.
[0021] The invention is a magnetostrictive displacement sensor, which is composed of a central control unit, a signal excitation circuit, a signal processing circuit, a high-speed timing circuit, an RS485 interface circuit, a power supply circuit and a waveguide wire; the RS485 interface circuit realizes the connection with external equipment. Communication and power supply circuits provide the required power for the sensor of the present invention. The information transmission of each part among the present invention is as follows:
[0022] 1. Central processing unit
[0023] In the present invention, the central processing unit adopts a cost-effective single-chip microcomputer (Atmega8L) to realize the control between each module in the magnetostrictive displacement sensor, wherein, the output excitation generation signal f 0 Give the signal to stimulate ...
PUM
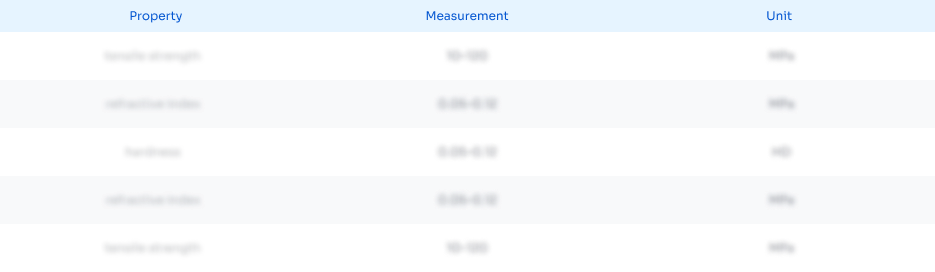
Abstract
Description
Claims
Application Information

- R&D Engineer
- R&D Manager
- IP Professional
- Industry Leading Data Capabilities
- Powerful AI technology
- Patent DNA Extraction
Browse by: Latest US Patents, China's latest patents, Technical Efficacy Thesaurus, Application Domain, Technology Topic, Popular Technical Reports.
© 2024 PatSnap. All rights reserved.Legal|Privacy policy|Modern Slavery Act Transparency Statement|Sitemap|About US| Contact US: help@patsnap.com