Thin-wall bimetal self-lubricating bearing and manufacturing method
A technology of self-lubricating bearings and manufacturing methods, applied in the direction of bearing components, shafts and bearings, mechanical equipment, etc., can solve the problems of low mechanical strength and high cost, and achieve the effect of improving mechanical strength, light weight and small volume
- Summary
- Abstract
- Description
- Claims
- Application Information
AI Technical Summary
Problems solved by technology
Method used
Image
Examples
Embodiment 1
[0017] a. Evenly spread 150-250 mesh spherical or dendritic copper alloy powder on a steel plate or stainless steel plate 1 of 1-3 mm, with a thickness of 0.5-2 mm, sinter in a hydrogen protection furnace or a vacuum furnace, and roll after sintering. Composite copper alloy layer 2 on steel plate or stainless steel plate 1;
[0018] b. On the copper alloy layer 2, process blind holes that can be circular, diamond-shaped, square, oval, etc. in various shapes by drilling, punching or rolling. The depth of the blind hole 3 is the same as the thickness of the aluminum alloy layer 2. The difference is 0.1 mm, that is, 0.4 to 1.9 mm. If it is a round hole, the diameter of the hole is 1.3 to 3.5 mm. It should be ensured that the total surface area of the solid lubricant accounts for 25 to 35% of the surface area of the copper alloy.
[0019] c. Spray ammonium chloride solution evenly on the inner surface of blind hole 3, spread 40-150 mesh spherical tin bronze powder on the ammon...
Embodiment 2
[0023] Others are the same as in Example 1, except that in step a, 150-250 mesh spherical or dendritic copper alloy powder is sprayed on the steel plate or stainless steel plate 1, and the copper alloy layer 2 is compounded on the steel plate or stainless steel plate 1.
PUM
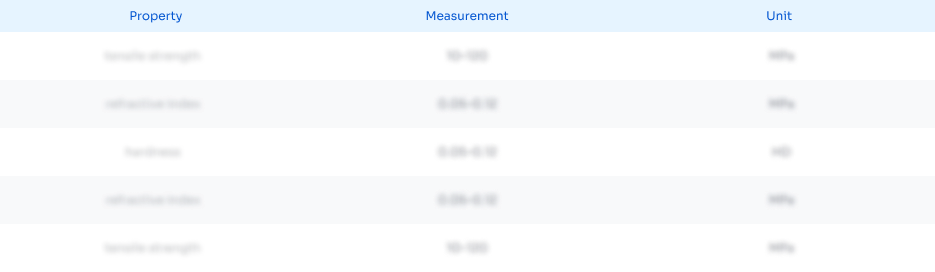
Abstract
Description
Claims
Application Information

- R&D
- Intellectual Property
- Life Sciences
- Materials
- Tech Scout
- Unparalleled Data Quality
- Higher Quality Content
- 60% Fewer Hallucinations
Browse by: Latest US Patents, China's latest patents, Technical Efficacy Thesaurus, Application Domain, Technology Topic, Popular Technical Reports.
© 2025 PatSnap. All rights reserved.Legal|Privacy policy|Modern Slavery Act Transparency Statement|Sitemap|About US| Contact US: help@patsnap.com